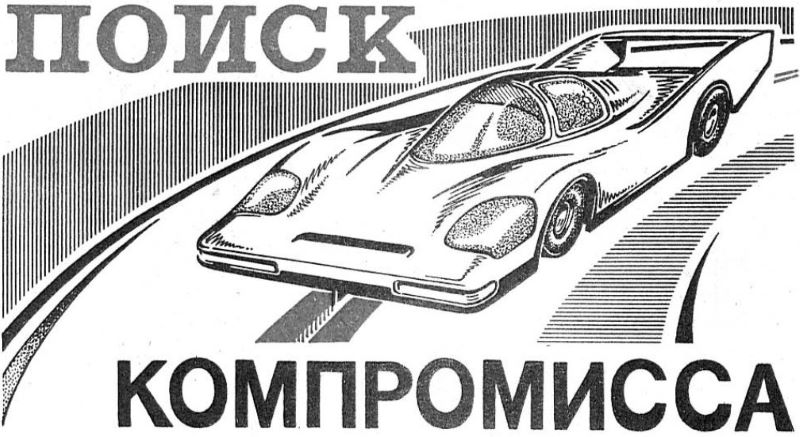
В «М-К» (№11, 1990 г.) были описаны модели автомобилей сильнейших трассовиков. Однако изготовление такой техники доступно далеко не каждому и обходится довольно дорого. А что делать спортсменам, не имеющим большого опыта, и начинающим кружковцам? Для них предлагается разработка модели автомобиля класса ТА-2 современной конструкции, но выполняемой из доступных материалов и без применения сложных технологий.
Рама модели автомобиля выпиливается из нефольгированного стеклотекстолита толщиной 2—2,5 мм. «Уши» (грузы-противовесы)— из латуни или стали толщиной 0,8—1 мм. Подвеска «ушей» люфтовая, ее устройство ясно из чертежа. Продольный и поперечный ход «уха» около 1,5 мм, вертикальный — порядка 2 мм по внешней кромке и минимальный по внутренней кромке в задней опоре. Передняя втулка имеет диаметр 2 мм, а стержень —1 мм.
Задний мост должен обеспечивать постоянное зацепление между шестернями. Для этого стойка подшипника со стороны шестерни делается с длинной опорной поверхностью, причем передняя заклепка выносится вперед от вала двигателя, который крепится на раме тремя винтами с потайными головками снизу. Пластмассовая ведомая шестерня (от электробритвы) растачивается и насаживается на диск колеса с натягом 0,15—0,2 мм. Диски колес — точеные, из дюралюминия или капролона. Шины: задние из материала импортных пляжных тапочек, передние — из пенополиуретана или пенополиэтилена.
Кузов модели автомобиля изготавливается из термопластичной пленки ПХВ, ПВХ, АБЦ или подобной методом вакуумной формовки (один из вариантов технологии уже был опубликован в «М-К»). В качестве прототипа можно использовать любой понравившийся автомобиль групп С1 и С2 выпуска после 1981 года — отклонение от масштаба оказывается в пределах допуска.
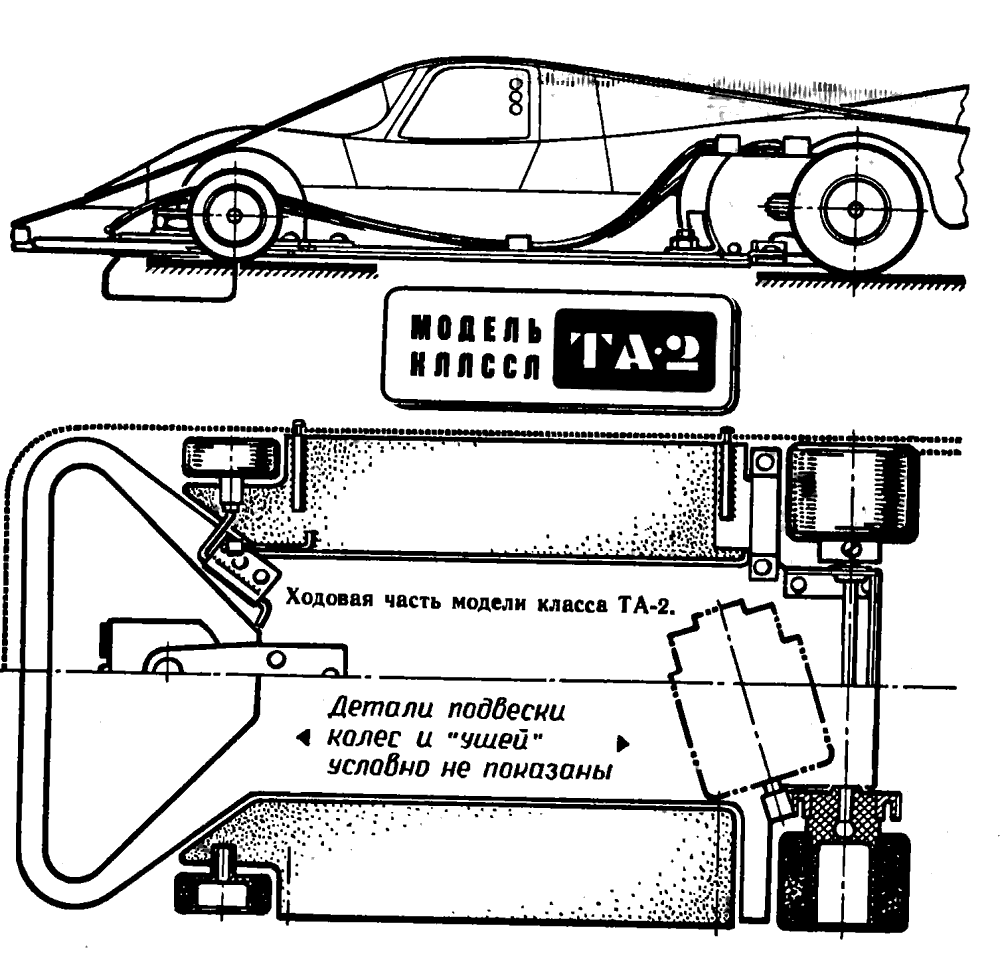
Теперь о наиболее сложной части модели автомобиля — двигателе. За основу взят мотор ДИ-1-2 (МПЗ-004). Правда, в результате модернизации от него остается немногое: корпус (частично), магниты (с доработкой) и железо якоря. Самостоятельно изготавливаются задняя крышка с щеточным узлом, гнездо переднего подшипника, вал, коллектор, обкладки и втулки якоря, обмотки.
Крышка вытачивается из сплава типа Д16Т, В95 или других, близких по твердости. Опиливается она (по размерам, взятым с чертежа в масштабе) уже после стыковки с корпусом.
Корпус нужно обрезать по длине и рассверлить отверстие под гнездо подшипника в передней стенке. Обе операции лучше выполнить на токарном станке. С обеих сторон от оси корпус симметрично спиливается до размера 17 мм. Затем присоединяют крышку и фиксируют ее винтами (четыре M1,6 или М2). Самая сложная операция — обжатие корпуса у передней стенки на 1,5 мм без деформации формы стенок, к которым прилегают магниты. Но провести эту работу необходимо, так как в стандартном исполнении зазор между якорем и магнитами составляет более 1 мм. Каких-либо приспособлений не понадобится, если обжим проводить в тисках, исправляя выгибающуюся переднюю стенку плоскогубцами. Потом припаивают лапы крепления двигателя на раме и гайки к ним. Монтаж мотора — на трех винтах. Широкая лапа — с двумя гайками со стороны задней оси; узкая — с одной гайкой с противоположной. Материал лап — латунь толщиной 0,5 мм или кровельное железо. Крышка спиливается по высоте, и в ней выполняются окна для щеточного узла. Выточенное из латуни или стали гнездо переднего подшипника запаивается на корпусе.
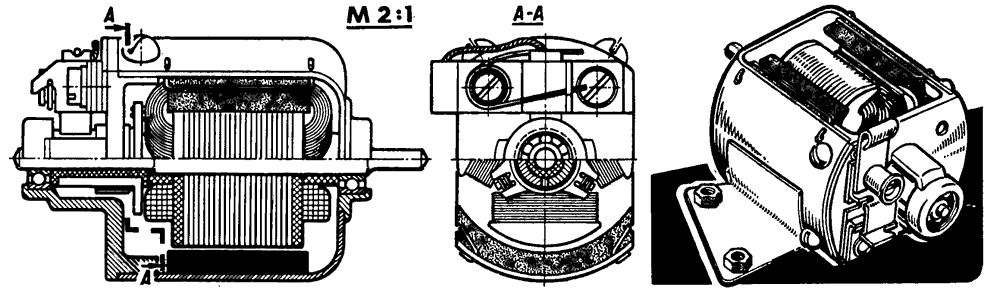
На магнитах нужно сошлифовать кромки, выступающие за пределы корпуса, причем не перегревая сам магнит и не охлаждая его в воде. Канавки, показанные на чертеже, пропиливаются алмазным надфилем либо тонким вулканитовым диском. Магниты монтируют с помощью эпоксидной смолы и скобок из мягкой проволоки.
Вал придется заменить на каленый из инструментальной стали диаметром 2 мм или на 3-миллиметровый из стали «серебрянки» (как его прошлифовать, видно на рисунках). Переходы от одного диаметра на другой не должны иметь острых внутренних углов, иначе возникнет высокая вероятность поломки вала.
Штатные пластины якоря при необходимости рассверливают. Пакет пластин и изолирующие накладки из стеклотекстолита толщиной 1 мм собираются на эпоксидной смоле с запрессовкой до полного отверждения связующего. Пазы якоря проклеиваются полосками кальки для изоляции. Между набором якоря и передним подшипником, а также между набором и коллектором ставятся текстолитовые втулки треугольного сечения. Их длина подгоняется так, чтобы якорь имел продольный люфт между подшипниками около 0,2 мм. Грани втулок опиливаются, чтобы удалось ровно уложить обмотки.
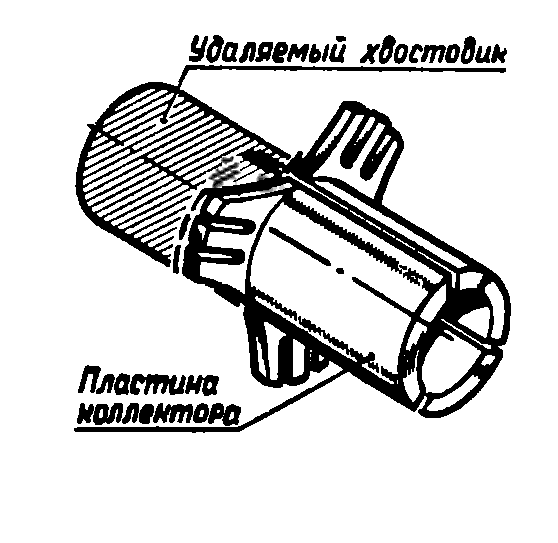
Изолирующая втулка коллектора с двумя фланцами вытачивается из текстолита, а заготовка для ламелей — из красной меди. После обработки последняя размечается для распила, по кулачкам патрона станка. При отрезании заготовки нужно оставить «хвост» длиной 5—7 мм, за который она зажимается при распиливании. Ламели и «рога» для обжима проводов выполняются лобзиком с пилкой по металлу, потом отделяется «хвост». Обжимное латунное кольцо — максимально допустимой ширины при толщине стенки 0,2—0,3 мм. Зазор между кольцом и ламелями Около 0,2 мм. При сборке ламели устанавливают на втулку, смазанную эпоксидной смолой, обматывают двумя-четырьмя слоями пропитанной смолой газетной бумаги и затем туго насаживают обжимное кольцо. Пока связующее не затвердело. с помощью тонкого шила выставляют зазоры между ламелями. Перед сборкой коллектора все его детали обезжириваются спиртом.
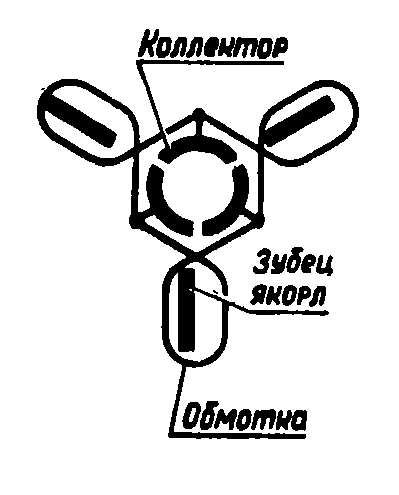
Схема обмотки показана на рисунках. Выполняется она проводом ПЭВ-2, ПЭТВ, ПЭТВ-2 диаметром 0,31—0,35 мм, по 60—70 витков. Нужно добиться полного единообразия обмоток, поэтому витки укладывают очень плотно. Полезно записывать число витков в каждом слое,) особенно при первых попытках изготовления двигателя. Если что-то не понравится или получится не очень удачно, обмотку обязательно снимают и выполняют заново. Готовые «катушки» пропитывают эпоксидной смолой (именно пропитывают, а не заливают!) и до отверждения якорь помещают в сушильном шкафу или вблизи лампы накаливания, коллектором вниз. Готовый якорь ставят на станок и протачивают коллектор.
Щетки выполняются из подобранного опытным путем материала. Их сечение 3X3 мм, причем в качестве заготовок лучше использовать щетки с выводом. Если таких нет, к торцу щетки проводник из достаточно толстого и мягкого «канатика» будет прижимать пружина. Щеткодержатели выгибаются из мягкой латуни толщиной 0,3 мм в простейшей оправке. Под ними ставят прокладки из стеклотекстолита 0,5 мм. Винты крепления изолируются от держателей текстолитовыми шайбами и фторопластовыми трубками. Пружины — из проволоки диаметром 0,5 мм, навиваются на стержне диаметром 3,2 мм, имеют 5 витков и при сборке одеты на стаканчики диаметром 3,5 мм. В месте прилегания к щетке на пружины поставлены фторопластовые трубки. Сила прижима зависит от материала щеток и коллектора, оборотов мотора, величины тока, качества балансировки, поэтому подбирается опытным путем. Двигатели, собранные по предлагаемой, технологии, удается «раскрутить» под нагрузкой до 35 000 об/мин.
Аналогичным методом можно переделать и другие электромоторы. Например, ДИ-1-3, или импортные, если они близки по конструкции.
Надо отметить, что ставить на текстолитовую раму мощные и динамичные двигатели с самарий-кобальтовыми магнитами не стоит: найти компромисс между характеристиками жесткости, массы и вибрационных свойств не удастся. В остальном же никогда не забывайте, что при создании модели мелочей нет!
А. НЕСТЕРЕНКО,
Ленинград
Источник: “Моделист-Конструктор” № 7, 1991, 24-25 с.
Оцифровка: masteraero.ru
Журнал: Моделист-Конструктор 1991-07.pdf