Это второй технический опыт Кена Ирвина из Cambridge Model Car Club в Кейптауне, Южная Африка.
Slotblog уже публиковал один из технических томов Кена “Как сделать резак для шин”, а вот следующий, “Blueprinting двигателей трассовых моделей”, который, на мой взгляд, является самой полной и глубокой диссертацией о двигателях трассовых моделей, которую когда-либо видел мир. Документ MS Word составляет 59 страниц и содержит 83 изображения!
Кен любезно предоставил ряд других технических руководств, которые в конечном итоге будут опубликованы здесь, на форуме Slotblog. Спасибо ему за то, что поделился своим огромным опытом и знаниями для улучшения нашего хобби.
Gregory Wells (Cheater с форума slotblog.net), 2014
Прим. ред.: Blueprinting означает означает полную переборку двигателя. Это процесс получения полноценного готового к гонкам двигателя из двигателя промышленного производства.
Имейте ввиду, что перечисленные методы “исправления” двигателя могут быть запрещены к использованию правилами или техническими требованиями соревнований, в которых вы собираетесь участвовать. Перед применением проконсультируйтесь с техническим специалистом.
Blueprinting двигателей трассовых моделей
Предупреждение: эта статья варьируется от простого к очень сложному и, возможно, даже возмутительному.
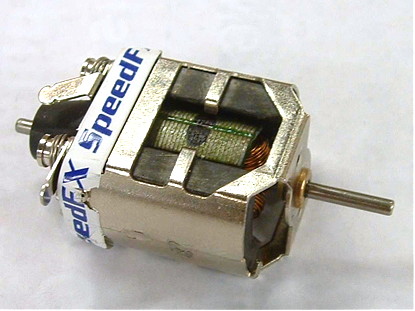
Blueprinting означает приведение двигателя в “blueprint” («чертеж») или в проектное состояние (а во многих случаях и в лучшее).
Эти двигатели производятся массово и имеют ряд «проблем», которые можно решить.
Примечание. Перед модификацией двигателя ознакомьтесь с местными/национальными правилами класса. Нет смысла выигрывать с помощью мошенничества или дисквалифицироваться после победы. Чем больше вы выигрываете, тем интенсивнее становится проверка вашей модели судьями.
Основные проблемы (в порядке важности/вероятности):
1) Плохое выравнивание ротора по магнитному полю двигателя (ротор сильнее прижат к одному или другому краю).
2) Незакрепленные магниты.
3) Незакрепленные подшипники скольжения.
4) Плохое выравнивание щеток.
5) Неидеальная балансировка ротора.
6) Неправильно изготовленный ротор – нет бандажа проводов.
7) Кривой коллектор.
8) Установка пружин прижима щеток.
9) «Дешевые» щетки и пружины.
10) Относительно «мягкие» валы роторов – при столкновении могут погнуться.
Приведенный выше список является «общим» и в той или иной степени применим ко всем моторам. Эти проблемы не относятся конкретно к Pro Slot SpeedFX (показанному на фотографиях), который, как правило, является прекрасным двигателем.
Следующий процесс blueprinting был выполнен для двигателя SpeedFX, но это применимо практически ко всем двигателям трассовых моделей.
Первые 17 шагов охватывают основы, а дальше все становится намного сложнее и техничнее.
Шаг 1 – Разберите двигатель
Выступ фиксатора пружины щетки должен быть слегка согнут внутрь, чтобы можно было «поддеть» конец пружины щетки небольшой отверткой. Он не должен быть согнут настолько сильно, чтобы вам приходилось разгибать его каждый раз, когда вам нужно снять пружину – если вы согнете этот язычок более двух раз, он сломается – так что сейчас самое время установить его правильно. Согните его внутрь или наружу по мере необходимости.
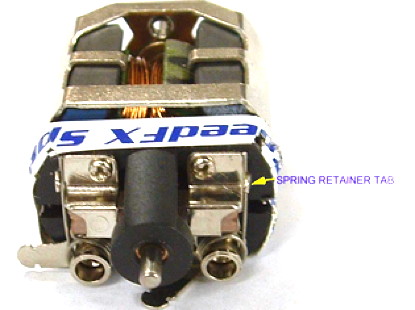
Вы также не хотите, чтобы конец пружины выходил слишком легко, иначе он может просто «выскочить» при столкновении.
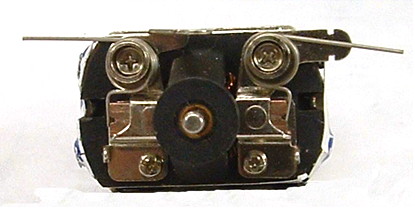
Отпустите пружины, стараясь не дать им вылететь (возможно, вы их больше никогда не увидите).
Убедитесь, что обе пружины установлены одинаково – на фото выше они разные (как было в комплекте). Если пружины сжимаются неравномерно, на подшипник воздействует боковая нагрузка, которая приведет к потере мощности.
Нормальная настройка — 90° (как для левой пружины выше), сгибайте до тех пор, пока обе пружины не станут одинаковыми.
Никогда не используйте несовпадающие пары пружин.
Некоторые люди предпочитают более «мягкую» настройку — то есть менее 90 ° — это уменьшает трение коллектора и контактное (токопроводящее) давление, поэтому это, очевидно, компромисс. По мере износа щеток этот угол в любом случае будет становиться все меньше и меньше.
Я предпочитаю сначала запускать двигатель с углом пружин 90°, а затем немного уменьшать угол – примерно до положения правой пружины на фотографии выше.
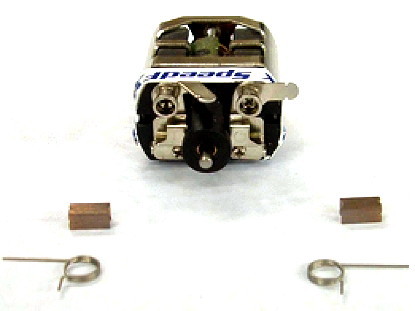
Снимите пружины и щетки. Примечание: пружины бывают левые и правые.
Примечание. Можно снять пружину задом-наперед — снимите край, упирающийся в щетку, затем витки со стойки и длинный конец с выступа. Это работает для сильно загнутых выступов.
Далее: Снимите наклейку-пломбу.
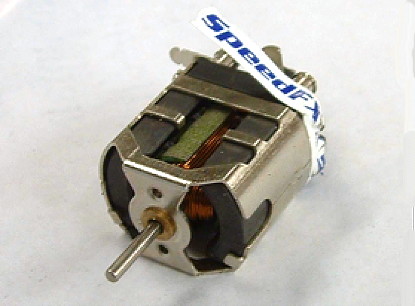
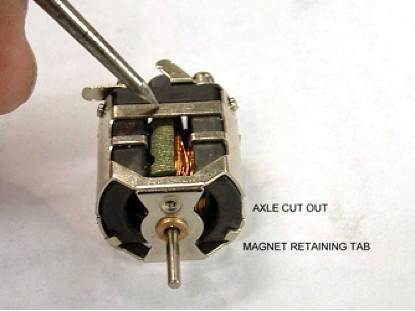
Отметьте “верхнюю” сторону – в данном случае это очевидно из-за выреза для оси модели в задней части стакана и магнитных упоров внизу. Но это не всегда так.
Вы же не хотите, чтобы статор был собран неправильно, так как в таком случае двигатель будет работать в обратном направлении (да, конечно, вы можете просто поменять провода местами, но это немного противоречит правилам “sealed motor” (“опломбированного” двигателя), если ваши провода подключены в обратном направлении).
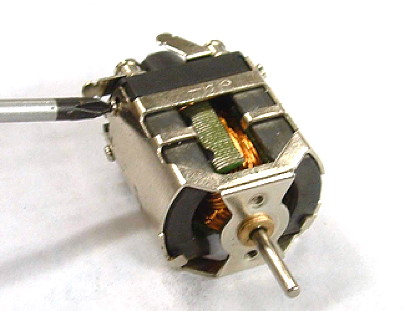
Открутите крепежные винты.
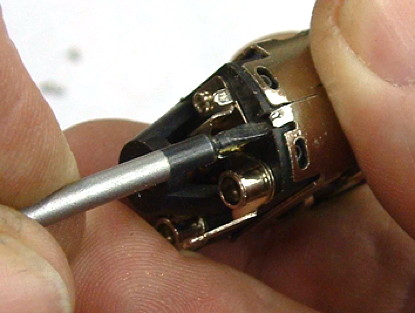
Если фиксирующие язычки загнуты, подденьте их небольшой отверткой. Если вы придерживаетесь правил “sealed motor” (“опломбированного” двигателя), вам нужно будет загнуть их обратно при сборке. Если же нет, то не беспокойтесь. Я обычно выгибаю их заподлицо со стаканом после разборки, если больше не собираюсь их использовать.
Снимите крышку и разберите двигатель.
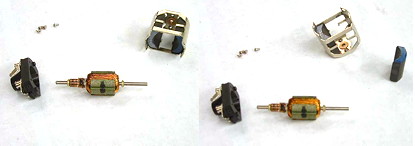
Примечание: Синий магнит и подшипник крышки просто вышли вместе с ротором, когда я разобрал двигатель – это та самая некачественная заводская сборка, которую мы и будем исправлять.
Примечание: Белый магнит находится слева (со стороны оси) – опять же, если вы поставите его неправильно, двигатель будет работать в обратном направлении при обычном подключении проводов, поэтому следите за этим.
Шаг 2 – Закрепите подшипники
Выньте подшипник скольжения из пластиковой крышки. Промойте подшипник, крышку и корпус двигателя в растворителе, например, в бензине. Старая баночка из-под 35-миллиметровой фотопленки отлично подходит для мойки двигателя трассовой модели.
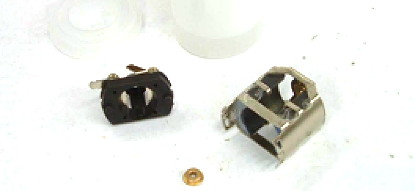

Используйте бутановую горелку для пайки переднего подшипника – припой проводите по внешнему краю. Следите за тем, чтобы припой не попал в отверстие подшипника – в противном случае он выйдет из строя и его придется заменить.
Совет: сначала нанесите припой на стенку стакана и дайте ему распределиться вокруг подшипника.
Если это разрешено вашими правилами, замените подшипник скольжения на подшипник качения (шариковый подшипник) и также припаяйте его на место. Шариковый подшипник – это метрический фланец MF52ZZ (KOYO, JAPAN или аналогичный). Что касается пайки шарикоподшипника, то сначала залудите его и отверстие в стакане двигателя с помощью паяльника и флюса, а затем припаяйте на место с помощью слабого пламени или большого паяльника – не допускайте “посинения” шарикоподшипника.
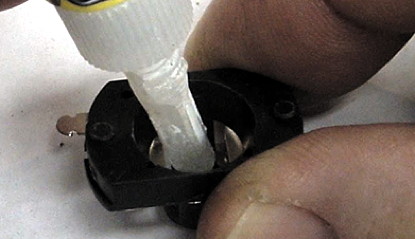
Нанесите каплю цианоакрилатного “суперклея” на посадочное место подшипника в крышке и плотно прижмите втулку на место. Так же будьте внимательны – не допускайте попадания суперклея в отверстие втулки.
Совет: Капните немного суперклея на обрезок медной проволоки и используйте ее как щуп для нанесения суперклея – так вы сможете избежать избытка клея.
Здесь также можно использовать шарикоподшипник, но обычно я не заморачиваюсь.
Шаг 3 – Проверьте выравнивание подшипников
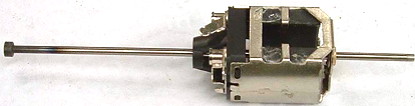
Проверьте соосность втулок с помощью стержня диаметром 2,0 мм. Здесь я использую выталкивающий штифт диаметром 2 мм (его можно приобрести у поставщиков оборудования, таких как Toolquip) – очевидно, вы можете просто использовать ротор – чтобы убедиться, что он свободно вращается.
Если он движется туго, попробуйте определить, с какого конца проблема, и с помощью штифта установите подшипник на место – в конечном итоге для устранения проблемы может потребоваться перепайка или повторная проклейка – Не используйте ротор в качестве монтировки.
Шаг 4 – Проверьте выравнивание щеткодержателей
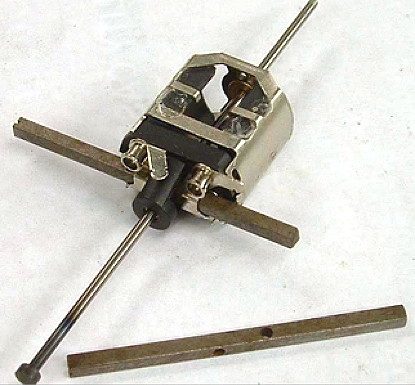
Используйте брусок для выставления щеткодержателей, чтобы обеспечить точное выравнивание щеткодержателей. Здесь необходимо использовать штифт диаметром 2,0 мм – по понятным причинам вы не можете использовать ротор.
Брусок представляет собой прямоугольную планку того же размера, что и щетка, с отверстиями диаметром 2 мм под прямым углом. Два отверстия – это на случай, если вы хотите установить щетки “горизонтально” (толстой стороной поперек коллектора) или “вертикально” (толстой стороной вдоль оси коллектора). Более подробно о щетках и углах опережения мы поговорим в конце статьи.
Вам также следует проверить, хорошо ли прилегают щеткодержатели к щеткам – регулировочная планка также позволяет сжимать или сгибать щеткодержатели для лучшей подгонки.
В идеале щетки должны свободно скользить с минимальным зазором, насколько это возможно.
Шаг 5 – Проверьте выравнивание ротора в магнитном поле
Вставьте магниты в стакан двигателя и плотно прижмите их к упорам. Они должны располагаться заподлицо с наружными торцами стакана и в одинаковом положении относительно друг друга – если нет, отогните один из упоров, чтобы магниты были установлены одинаково.
Свободно соберите стакан, ротор и крышку (винты заменять не нужно).
Поверните ротор пальцами и дайте ему возможность свободно вращаться и остановиться.
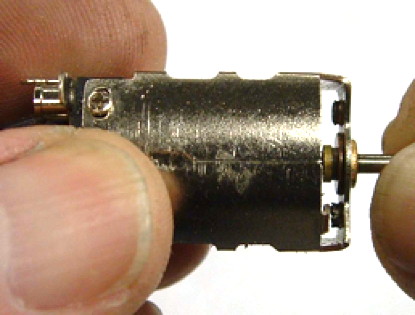
Толкните вал ротора внутрь, чтобы проверить, есть ли зазор между ротором и подшипником в крышке. Затем толкните со стороны крышки, чтобы проверить, есть ли зазор между ротором и подшипником стакана.
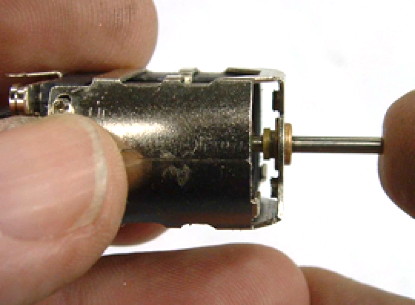
Мы хотим, чтобы ротор вращался и самоцентрировался внутри магнитного поля и останавливался с зазором 0,1–0,25 мм (плавающим) на обоих концах.
Мы не хотим, чтобы он терся с обоих концов.
Помните, что во время работы двигателя его ротор будет сильно тянуться к магнитной осевой линии, и если этому помешать, он будет сильно упираться в один из подшипников. Это приведет к потере мощности из-за трения.
Если ротор сильно прижимается к подшипнику стакана, как в случае на фотографии выше, нам нужно сдвинуть упор на самом роторе еще ближе к обмоткам. Но сначала нам необходимо проверить положение коллектора относительно щеткодержателей.
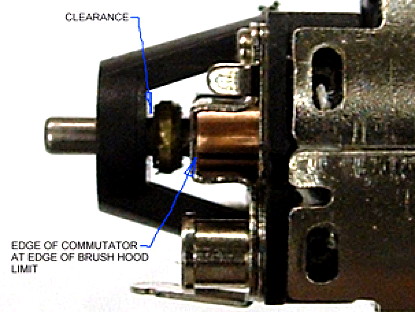
На фотографии выше зазор (clearance) в крышке чрезмерный. Для уменьшения зазора я уже выдвинул внешнюю проставку до конца и не могу больше двигать ее дальше, иначе щетки вылетят за край коллектора.
Если вы получили такой же результат, тогда вам необходимо сдвинуть магниты в сторону крышки, пока вы не получите небольшой зазор между ротором и подшипником крышки во время вращения ротора, когда ротор стремится к центру магнитного поля.
Если с зазором в крышке все в порядке, то для увеличения зазора в стакане необходимо сдвинуть упор с соответствующей стороны.
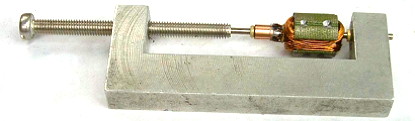
Фото выше — регулировка проставки с помощью инструмента для запрессовки шестерни на вал ротора.
Сдвигайте упор на роторе со стороны стакана постепенно, проверяя при каждой регулировке зазор или пока не достигнете предела, установленного краем коллектора.
Если же вам нужно переместить магниты ближе к крышке, сделайте это, согнув язычок, удерживающий магнит, с помощью оправки и молотка, как показано на фотографии ниже.
Убедитесь, что вы делаете одинаково с обеих сторон и делаете это постепенно, проверяя после каждой регулировки.
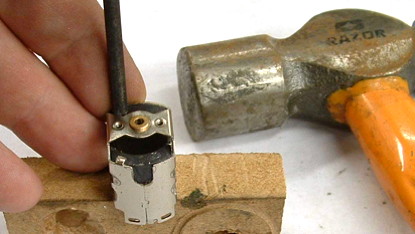
Отогните язычки, удерживающие магниты, назад (при необходимости), чтобы переместить магниты назад.
После получения зазора возле подшипника стакана нам нужно установить зазор возле подшипника крышки. В этом случае упор необходимо выдвинуть наружу (что намного сложнее, чем внутрь).
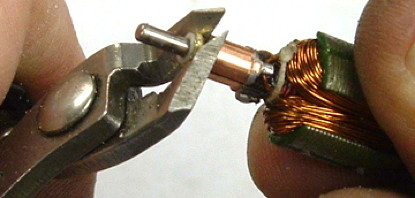
Сдвинуть его можно, используя острую пару диагональных кусачек в качестве клина. В качестве альтернативы можно использовать шайбы, что будет безопаснее.
Примечание. В этом двигателе используется комбинация вставной проставки и упорной шайбы. В некоторых двигателях просто используются свободные проставки. При использовании прокладок сразу за коллектором всегда должна находиться фенольная (пластиковая) прокладка.
Очевидно, сначала вам необходимо отрегулировать наиболее «плотный» конец; в данном случае это был конец со стороны стакана, но это мог быть и конец со стороны крышки.
Подбор проставок под двигатель.
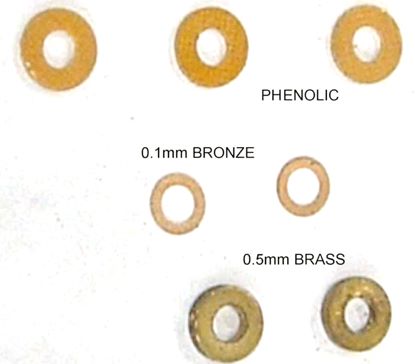
Шаг 6 – Приклейте магниты на место
Как только вы убедитесь, что у вас есть свободный проход на обоих концах ротора (от 0,1 до 0,25 мм на каждом конце и около 0,3-0,5 мм общего “зазора”), пришло время приклеить магниты на место с помощью суперклея. После всех этих усилий по выравниванию мы не хотим, чтобы магниты сдвинулись с места в случае аварии.
ВНИМАНИЕ: Прежде чем делать это, наденьте латексные перчатки или нанесите на руки защитный крем – особенно если вы использовали обезжириватель – очищенная кожа может навсегда приклеиться суперклеем. Пожалуйста, будьте осторожны! Вы можете слишком сильно привязаться к своему хобби.
Нанесите суперклей на все края вокруг магнитов.
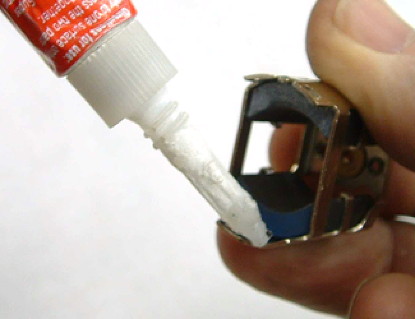
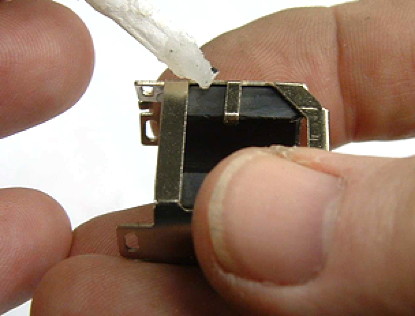
Приклейте везде, где только сможете добраться. Дайте клею затвердеть.
Если на этом этапе у вас возникнут какие-либо блестящие идеи об использовании клея для размещения магнитов ближе к ротору для большей производительности (тем самым уменьшить магнитный зазор) – вы безнадежно ошибетесь – см. подробное объяснение позже, а также советы по установке прокладок и т. д.
Сейчас самое время для намагничивания (zap) магнитов (см. ниже).
Шаг 7 – Настройте ротор
Итак, это ваш ротор
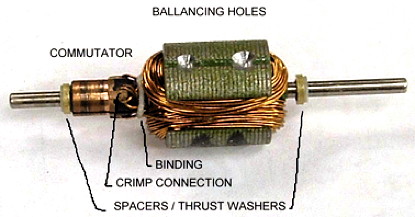
Мы собираемся сделать следующее – в таком порядке:
1) Установите проставки (как было указано выше).
2) Проверьте/установите «timing» (угол опережения коллектора).
3) Пропаяйте коллектор.
4) Сделайте бандаж коллектора (если он отсутствует).
5) Замените вал (если он сильно погнут и это стоит затраченных усилий).
6) Отбалансируйте ротор.
7) Проточите коллектор.
Шаг 8 – Угол опережения коллектора
См. позже более подробное объяснение того, почему двигателю трассовой модели требуется опережение коллектора, а пока – для Группы 16D вам нужно опережение примерно на 25-30°; для Группы 12 требуется опережение примерно на 45°.
Ноль градусов — это когда зазоры в коллекторе совпадают с центром полюсов якоря.
Расширенный вариант — это когда зазоры смещены против часовой стрелки (направление вращения двигателя, если смотреть со стороны коллектора).
Примечание. Это верно только в том случае, если щетки лежат в той же плоскости, что и магниты. Это не относится к таким двигателям, как NC5 и 6, у которых щетки расположены под углом к магнитам, а также имеют смещенные обмотки.
Вам понадобится угломер – вот он…
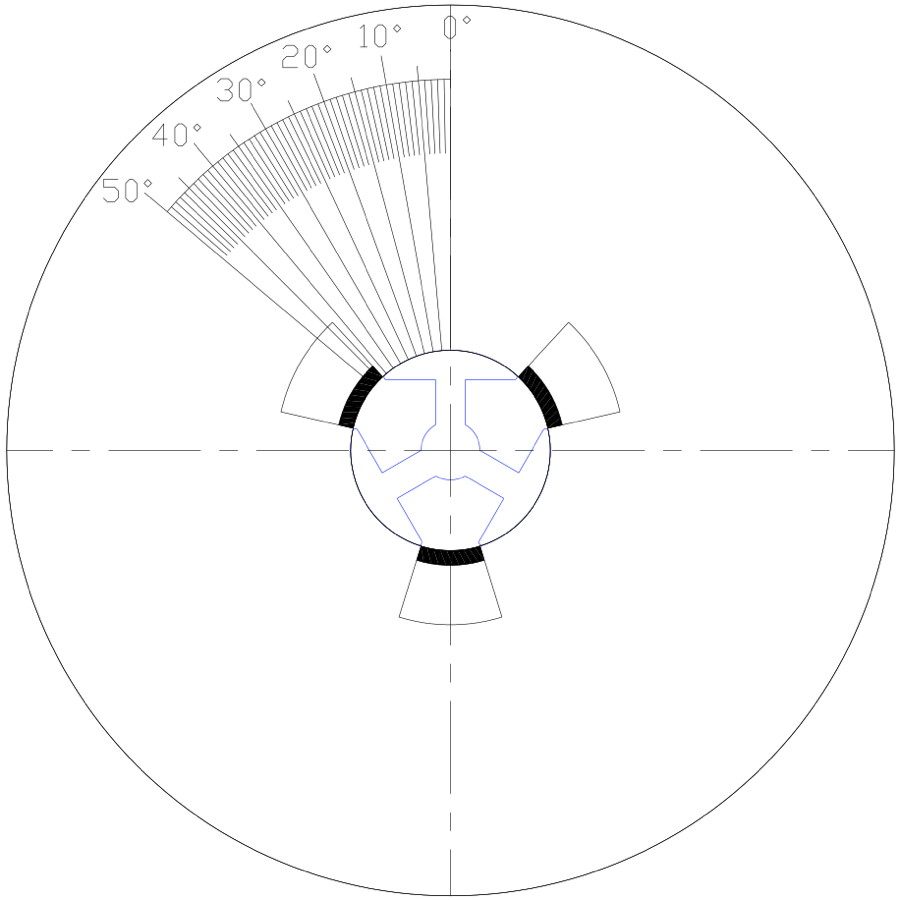
Наклейте его на кусок картона и проделайте посередине отверстие, подходящее для ротора. Или вы можете пойти дальше и приклеить его к куску алюминия диаметром 60 мм., отверстием 13,5 мм, толщиной 10 мм и торцевым отверстием для крепежного винта M5 под углом 0°.
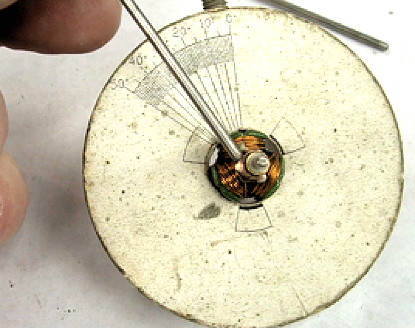
Установите ротор в ноль по мертвой точке полюса (иногда имеется канавка для маркера, как в этом случае) или симметрично выровняйте маркеры по зазорам. Используйте линейку, чтобы снять показания от канавки коллектора до параллельной линии на угломере – при взгляде прямо назад. (Эта фотография смещена от центра, поэтому вы не можете правильно увидеть, что линия выровнена под углом 29°)
Внимание: измерение – это одно, а регулировка – другое.
Регулировка может привести к разрушению коллектора, обрыву проводов и т. д. Выбросьте ротор – не пытайтесь отрегулировать, если регулировка действительно необходима или если вы не уверены, что сможете это сделать (и что хотите это сделать).
Регулировка: сначала убедитесь, что провода, идущие к коллектору, имеют достаточный провис, чтобы можно было выполнить регулировку. Если ваш ротор «связан» бандажом (фиксирующим эти провода), вам придется снять бандаж и поставить новый после регулировки.
Далее: Попробуйте покрутить коллектор пальцами – это самый безопасный метод. Если вы не можете сделать это легко, подумайте о том, чтобы сдаться или перейти к более жестким методам.
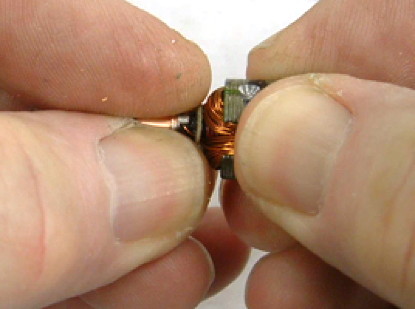
Используйте патрон, чтобы захватить коллектор за диаметр основания (который немного больше, чем рабочая поверхность коллектора), при этом повернув его к точкам разъема.
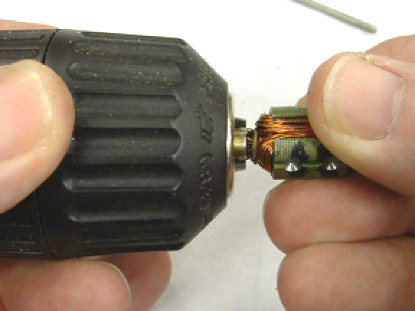
На фотографиях выше бандаж коллектора все еще на месте (фото только для демонстрации).
Двигайтесь небольшими шагами, часто проверяйте, не слишком ли туго натянуты провода.
При паяных коллекторах иногда целесообразно отпаять провода, произвести необходимую регулировку, а затем перепаять их.
Шаг 9 – Пропаяйте коллектор
Из–за идиотских законов о сокращении количества свинца (Внимание: этот продукт может содержать вещества, вредные для беременных женщин – я знаю, что беременным женщинам хочется есть, но я никогда не слышал, чтобы кто-то ел ротора трассовых моделей), провода многих роторов соединены с коллектором с помощью обжима, что неизбежно приводит к плохим соединениям.
Я вырос в доме со свинцовой сантехникой, и это нисколько на меня не повлияло – просто спросите любое из говорящих растений, которые ходят за мной по пятам весь день.
Внимание: Не паяйте коллектор, если у вас нет доступа к оборудованию для проточки коллектора, например, к токарному станку, станку для проточки коллекторов Hudy или аналогичному оборудованию. (Оно понадобится вам при пайке).
Чтобы пропаять коллектор, вам понадобится высокотемпературный припой.
Есть две проблемы: его может быть трудно достать, и он плохо паяется.
Вот совет: просверлите кусок свинца и оставляйте нити свинцовой стружки.
Паяйте своим любимым припоем и флюсом, а затем добавляйте свинцовую нить до тех пор, пока припой не перестанет впитывать свинец – теперь вы повысили температуру плавления (добавив свинец) практически до того уровня, на который способен ваш паяльник.
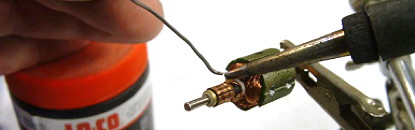
Изготовление свинцовой стружки для добавления в припой.
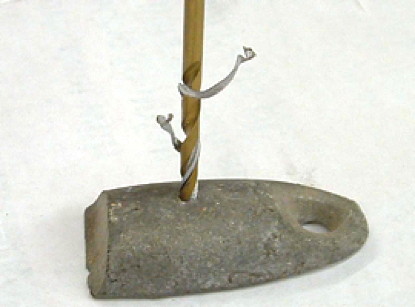
Добавьте свинец в припой. Либо, добавьте высокотемпературный припой после лужения, используя сначала наиболее удобный для вас припой/флюс.
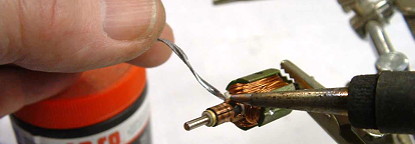
Припой почти всегда попадает на рабочую поверхность коллектора, поэтому после пайки требуется проточка коллектора на станке. Что бы вы ни делали, не заливайте припоем прорези – его будет очень сложно соскрести.
Шаг 10 – Добавьте бандаж
Бандаж или обмотка проводов за коллектором не позволяет им сгибаться при каждом цикле вращения вверх-вниз, что в конечном итоге сгибает их до разрыва.
Если ваш ротор не имеет бандажа – перевяжите его териленовым или вискозным шнуром (материал, который используют для «хлеста» удочек, продается в любом магазине снастей).
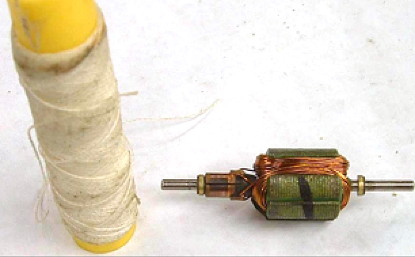
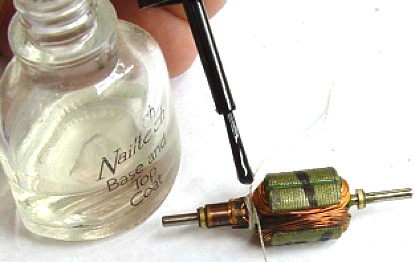
Сделайте узелок (4-5 витков в зависимости от толщины), покройте лаком (подойдет прозрачный лак), дайте высохнуть, затем обрежьте концы.
Примечание. Лакирование также помогает повторно закрепить бандаж, если вы его переместили. Если вам кажется, что коллектор плохо закреплен на оси, вы можете нанести немного суперклея на заднюю часть коллектора перед бандажированием и лакированием.
Если вы привередливы, используйте прозрачный лак для роторов General Electric «Glyptal», который специально создан для данного применения — если вы можете его достать (он поставляется в канистрах по 5 литров).
Осмотрите обмотки на наличие незакрепленных витков (они будут двигаться и в конечном итоге сломаются), и если они обнаружены, покройте их лаком, чтобы зафиксировать на месте.
Шаг 11 – Замените вал двигателя
При столкновении вал может погнуться. Его можно заменить, вытолкнув старый вал на новый (используйте выталкивающий штифт диаметром 2,0 мм из строительного магазина – отрежьте до нужной длины).
Это не так просто, как кажется — вам понадобится специальный инструмент, чтобы все было ровно и чтобы не допустить деформации валов.
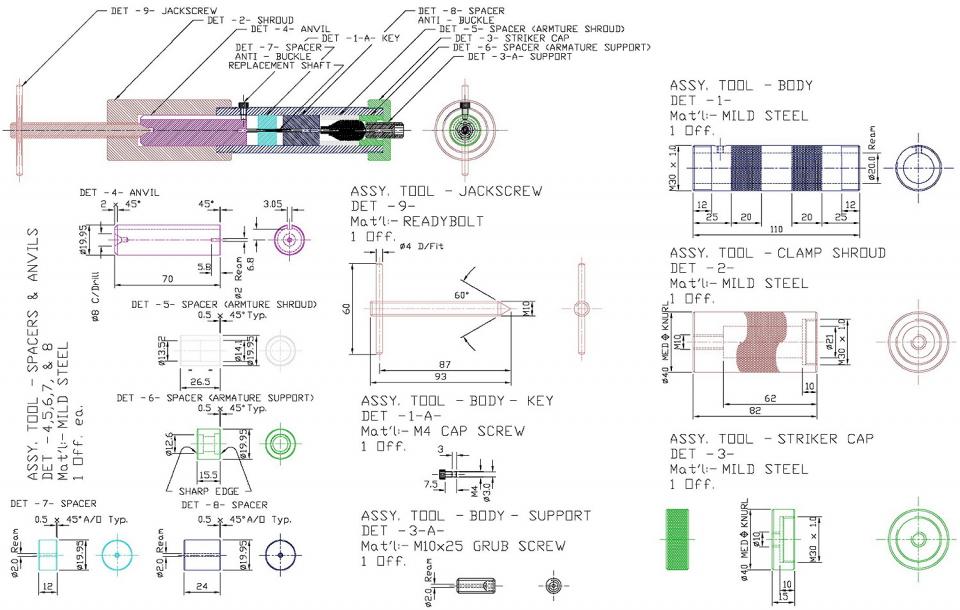
Сначала вы устанавливаете обе (короткую и длинную) распорки для предотвращения прогиба – когда они станут длиннее, снимаете короткую, когда они снова станут длиннее, меняете длинную на короткую и, наконец, после того, как они станут длиннее, снова снимаете короткую и завершаете сборку. Это предотвратит прогиб сменного вала под нагрузкой при установке (особенно при плотной посадке).
Примечание: Деталь 3А поддерживает нижний конец (распорную трубку или что–то еще) ротора и должна просто упираться в него, когда якорь прижат к детали 6 – опоре ротора.
Деталь 4 со шпоночным пазом очень важна для предотвращения вращения (деталь 1А – в этом пазу проходит шпонка) – без нее вы провернете коллектор (вы можете догадаться, как я это вычислил).
Детали 5 и 6 имеют концы разного диаметра для охвата/поддержки роторов разного диаметра.
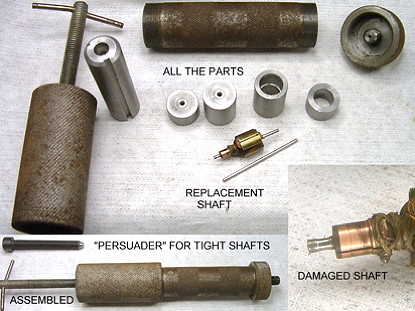
На фото выше ротор PS700B был поврежден из-за отсутствия смазки задней втулки скольжения – после замены вала и проточки коллектора он стал как новый.
Шаг 12 – Балансировка ротора
Статический против динамического баланса
Если вы просто добавляете или убираете вес с несбалансированного объекта до тех пор, пока он не перестанет возвращаться к центру тяжести, это называется «статическим балансом». Очевидно, что вы, вероятно, не добавили или не удалили вес ровно напротив ошибки. Поэтому, когда ротор вращается на высокой скорости, он все равно будет в некоторой степени разбалансирован.
«Динамический баланс» достигается путем вращения объекта на скорости и анализа (на сложной машине) количества и местоположения ошибок, чтобы их можно было исправить для движущегося объекта.
Из этого следует, что динамически сбалансированный объект также статически сбалансирован (но не наоборот).
Ротора этих двигателей динамически сбалансированы, но, поскольку это массовое производство, процесс балансировки, как правило, несовершенен.
Динамическая балансировка – это далеко не то, что вы можете сделать в домашних условиях. (Хотя в сети есть много чертежей самодельных установок, так что это возможно).
Поэтому мы выбираем статическую балансировку, понимая, что если ротор не сбалансирован статически, то он также не является правильно сбалансированным динамически, и любое улучшение, которое мы делаем статически, все равно должно быть лучше, чем оставить все как есть.
Балансировка на лезвиях Stanley Knife делается так:
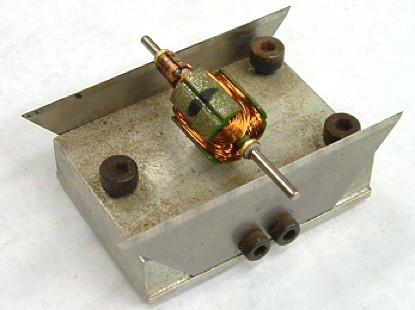
Вы можете изготовить блок из плотной древесноволокнистой плиты (см. чертежи). Три выравнивающих винта используются для устранения любого наклона или перекоса.
Используйте совершенно новые лезвия и будьте осторожны, чтобы не уронить на них ротор – устанавливайте его на место очень аккуратно, иначе на острых кромках останутся вмятины, которые будут мешать поведению ротора.
Выровняйте ротор так, чтобы он не перекатывался сам по себе.
Дайте ротору слегка повернуться (толкните его) – если у него есть тяжелая сторона, он всегда будет возвращаться в одно и то же положение. Для проверки толкните его несколько раз.
Если вы можете точно определить тяжелую сторону, снимите ротор с ножей и просверлите материал с тяжелой стороны.
Примечание: если один из полюсов направлен вверх, а два вниз, необходимо просверлить оба “тяжелых” полюса.
Используйте сверло диаметром 3 мм – если в этом полюсе уже есть два отверстия, удалите материал поровну из обоих. Не углубляйтесь слишком глубоко (максимальная глубина параллельной части – 0,5 мм). Если вам нужно удалить больше, просверлите третье отверстие между двумя имеющимися. Если вы просверлите слишком глубоко, керн может сломаться на высоких оборотах двигателя.
Удаляйте материал в очень небольших количествах, часто проверяя балансировку. Повторяйте процедуру до тех пор, пока ротор не будет останавливаться в любом положении.
Вы можете дополнительно «точно настроить» баланс, добавив вес — просто добавьте немного лака на «легкие» боковые обмотки — и повторяйте до тех пор, пока не добьетесь баланса.
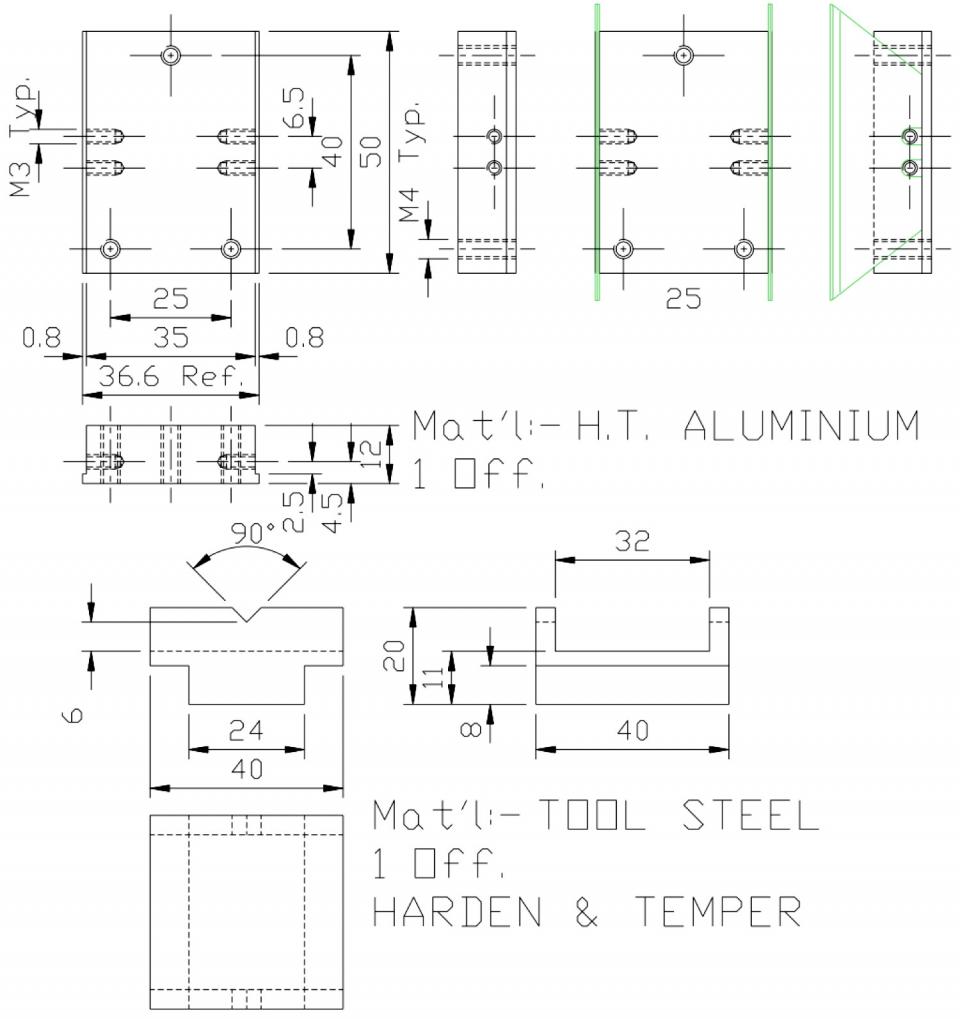
Внимание: Храните блок с лезвиями в безопасном месте или контейнере, когда не используете. Эти острые лезвия представляют реальную опасность, если их просто оставить лежать где попало.
Шаг 13 – Отбалансируйте ротор с помощью молотка (???)
Если вы просто проверяете старый ротор, который, как вы точно знаете, был отбалансирован, но теперь разбалансирован (особенно если он сильно разбалансирован), то вал ротора погнут.
Примечание. Небольшие изменения в балансе являются нормальными из-за размягчения лакового покрытия обмотки при нагревании и некоторого смещения обмотки во время горячего использования. Если есть сомнения, проверьте биение с помощью индикатора. Не используйте этот метод, если вы не уверены, что вал погнут.
Поскольку он был в равновесии, мы можем исправить его, отогнув его назад – ударяя небольшим молотком по подходящей наковальне, пока мы не вернем его в равновесие, после чего вал снова должен стать прямым.
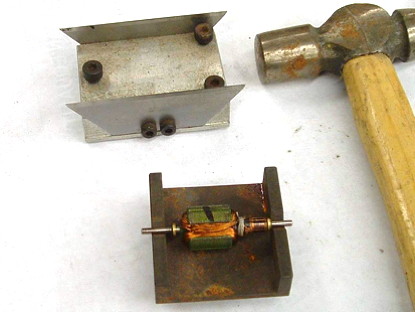
Ударьте по ротору на наковальне (тяжелой стороной вверх), а не на лезвиях.
Если вы приблизились к балансу – прекратите бить (маловероятно, что вам когда-нибудь удастся добиться полного баланса чем-то столь жестоким, как молоток) и приступайте к сверлению, чтобы вернуть баланс.
Шаг 14 – Проточите коллектор
Когда коллектор был изготовлен, он, вероятно, был обработан алмазом каким-нибудь загадочным восточным джентльменом на фабрике в Ванкинге.
К сожалению, после всех сложностей при сборке, ошибок в процессе сборки вала и т.д., коллектор почти наверняка уже не совсем соответствует качеству к тому времени, когда он выходит из рук производителя двигателя (дорогостоящие/качественные ротора подвергаются обработке после сборки).
Также к настоящему моменту у нас есть припой на рабочей поверхности коллектора, так что в целом нам нужно проточить его, чтобы вернуть в исходное состояние.
Для этого вы можете использовать станок для проточки коллекторов Hudy или, мой личный фаворит, настольный токарный станок.
Вам понадобится очень острый режущий инструмент из быстрорежущей стали или синдита (синтетического алмаза) с большим боковым срезом, отшлифованный почти до блеска на очень тонких дисках. Используйте этот инструмент только для проточки коллекторов.
Вам также понадобятся зажимная втулка (clamp bush) и втулка задней бабки (tailstock bush) – см. фото ниже.
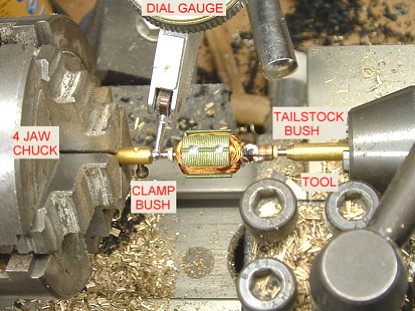
Установите зажимную втулку (clamp bush), закрепите ротор в четырехкулачковом патроне и отрегулируйте с помощью индикатора часового типа (dial gauge).
Пропустите конец коллектора через направляющую трубку (tailstock bush) (кусок латунного стержня диаметром 5 мм, рассверленный до 2,0 мм) в сверлильном патроне задней бабки. (Вы также можете использовать подшипник скольжения двигателя в сверлильном патроне задней бабки, но доступ для резца может стать проблемой.)
Нанесите кистью парафин или скипидар в качестве смазки и вращайте со скоростью 2000 об/мин, делая очень легкие проходы резцом, пока коллектор не очистится.
Во время проточки рабочей поверхности коллектора, вы можете увидеть, насколько плохой она была до очистки.
Если вы сделаете это правильно с помощью заточенного инструмента, канавки не потребуют удаления заусенцев. Если необходимо снять заусенцы, используйте острый нож Exacto и заостренную зубочистку, чтобы очистить канавки.
Окончательно отполируйте его бумагой с зернистостью 1200 с парафином или скипидаром в качестве смазки. Не используйте какую-либо химическую полировку коллектора – он может выглядеть хорошо, но остатки химикатов не удаляются, а коллектор мгновенно чернеет и сгорает до хрустящей корочки. Вы были предупреждены!
Наконец, очистите ротор обезжиривателем, и все готово.
Проточка коллектора, как правило, не приводит к нарушению балансировки (если только в процессе вы не удалили слишком большой кусок припоя), поэтому вы можете просто вернуть его на балансировочный стенд для окончательной проверки.
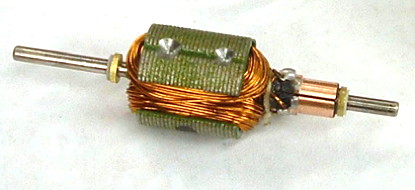
Наш готовый выставленный по зазорам, бандажированный, пропаянный, отбалансированный и проточенный ротор. Чтобы избавить себя от всех этих хлопот, вы можете купить готовый “blueprinted” ротор, однако вам все равно придется выставить зазоры.
Ниже показан ротор Pro Slot “blueprinted” – почти идеальный – вы ничего не сможете сделать, чтобы улучшить его.
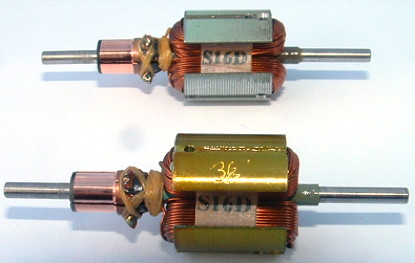
Выше ротор Pro Slot PS700B (“Big Dog”) – намотка на станке с ЧПУ, тонкие пластины – это совершенство и произведение искусства.
Примечание. Большинство правил допускают «стандартный» ротор группы 16D, который представляет собой 60 витков провода 28 AWG. Большинство правил также допускают использование ротора Pro Slot PS700B (“Big Dog”), который состоит из 55 витков провода 30 AWG и работает с большим углом опережения коллектора 36 ° — этот ротор обычно требует, чтобы вы сделали что-то для увеличения силы контура магнитного поля — см. ниже — что может быть не разрешено.
Шаг 15 – Вырежьте зазор для оси в задней части двигателя
В начале я мог бы предупредить о необходимости соблюдать чистоту и, в частности, избегать попадания железных опилок на двигатель – все в порядке, пожалуйста, делайте это.
Но следующий шаг приведет к беспорядку, и с этим ничего не поделаешь, поэтому нам все равно придется убирать перед сборкой.
Задняя часть двигателя в большинстве случаев загрязняет заднюю ось (несмотря на вырез в стакане), поэтому мы обычно шлифуем здесь канавку. Лучше всего это делать при разобранном моторе – из закрытого мотора сложно вытащить весь мусор.
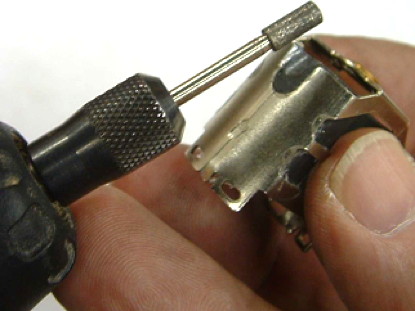
Прошлифуйте магнит с помощью шарошки с алмазным покрытием и дремеля. Вы также можете сделать это на уголке шлифовального круга, но это не так аккуратно.
Сжатый воздух обычно удаляет всю грязь – если у вас нет источника воздуха, используйте липкую шпаклевку, чтобы удалить всю пыль, прилипшую к магнитам.
Не могу сказать, что я когда-либо замечал снижение производительности при шлифовании магнитов таким способом.
Шаг 16 – Приточите щетки двигателя
Щетки двигателя имеют лишь частичную форму под коллектор (в некоторых случаях они совсем плоские) – мы не хотим часами катать в двигателе эти чертовы штуки, чтобы они притерлись, поэтому мы их шлифуем – так мы заставим их соответствовать форме коллектора.
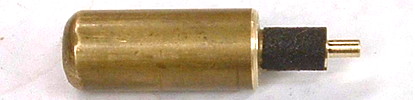
Сначала сделайте щеточный “напильник” – вы можете купить такие вещи, но они легко изготавливаются. Как показано на фотографии, отрежьте оправку с направляющим стержнем диаметром 2 мм и диаметром, соответствующим вашему коллектору, за вычетом толщины наждачной бумаги № 600, которую вы собираетесь приклеивать контактным клеем. Готовый диаметр должен соответствовать диаметру вашего коллектора.
Отрежьте кусок наждачной бумаги и подрезайте до тех пор, пока он не будет идеально подходить по размеру – нанесите клей и закрепите резинкой – дайте высохнуть.
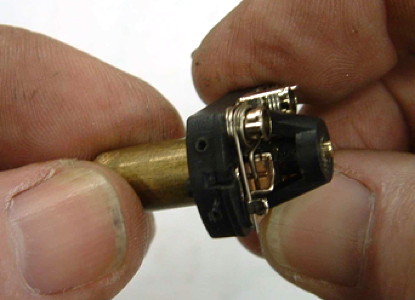
Установите в крышку, соберите щетки и пружины и вращайте вручную, чтобы приточить щетки – часто проверяйте.
Для этого вам не нужно разбирать двигатель при замене щеток – держите под рукой старую (но правильно выровненную) крышку как раз для этой цели.
Обязательно верните щетки на место таким же образом для дальнейшей шлифовки или сборки. Для этой цели на каждой щетке можно нацарапать небольшую опознавательную метку – я обычно помечаю их знаками – и + в направлении контактного выступа.
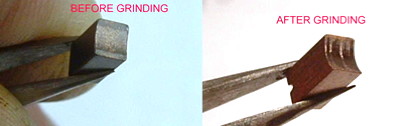
Шаг 17 – Соберите двигатель
При замене крепежных винтов постарайтесь повторно зацепить исходную резьбу — конечно, они сами нарежут новую резьбу, но сорвать ее будет гораздо легче, особенно если вы сделаете это несколько раз.
Нанесите каплю масла на каждый подшипник, не переусердствуйте. Я использую масло для автоматических трансмиссий (ATF).
Шаг 18 – Запустите двигатель
Если вы не протачивали коллектор, то, возможно, было бы разумно не шлифовать щетки и запустить двигатель в течение часа при напряжении 3-5 вольт, часа при напряжении 6-10 вольт и после этого в течение нескольких минут поднимать и опускать напряжение.
Если вы проточили коллектор и приточили щетки, запустите двигатель на 5 минут при напряжении 5-6 вольт и после этого в течение нескольких минут поднимайте и опускайте напряжение.
Вот оно.
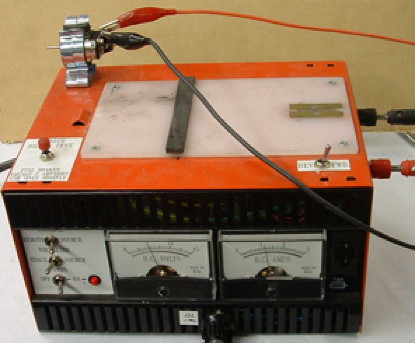
Шаг 19 – Полюбуйтесь своей работой
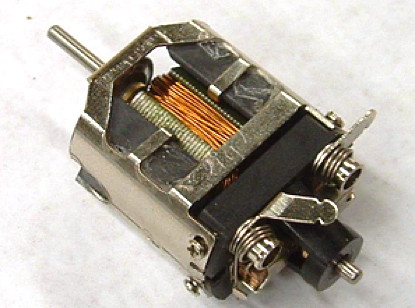
Черт возьми, после всех этих усилий он не выглядит иначе, но поверьте мне, он полетит как пуля.
Пропуски и дополнительные темы
Есть пара моментов, которые я не рассмотрел в Blueprinting, поскольку они, как правило, “запрещены” для гонок в классе 16D, но я расскажу о них сейчас.
1) Проверка центровки подшипника стакана – некоторые люди делают из этого большую проблему. Лично я не считаю это проблемой. Конечно, вы, очевидно, хотели бы, чтобы ваш ротор располагался ровно в центре, симметричном магнитам, но если вы продолжите читать, то поймете, почему это не так уж важно (положение ротора внутри поля не окажет большого влияния на общую силу магнитного “контура”).
2) Магнитные прокладки для увеличения силы магнитного контура. Использование “направленных” четырехполюсных (или более) магнитов.
3) Шунтирование щеток двигателя.
Очевидно, что пункты 1 и 2 идут рука об руку, но если речь идет о гонках в классе 16D, это выходит за рамки “blueprinting”, возможно, в область “читерства” – в зависимости от правил вашего клуба.
Перед модификацией двигателя ознакомьтесь с местными/национальными правилами класса. Нет смысла выигрывать с помощью мошенничества или дисквалифицироваться после победы. Чем больше вы выигрываете, тем интенсивнее становится проверка вашей модели судьями.
Теперь ознакомьтесь с нижеследующим, чтобы получить более полное представление о том, как работает двигатель трассовой модели. Это понимание поможет вам принимать более взвешенные решения.
Двигатели трассовых моделей
Щеточно-коллекторный узел и угол опережения – все, что вы когда-либо хотели знать (и, вероятно, многое из того, чего вы не знали).
Зачем двигателю трассовой модели нужен усовершенствованный коллектор и насколько он должен быть усовершенствован?
Полное техническое описание проблемы слишком ужасно, чтобы его рассматривать, оно затрагивает такие сложные темы, как hysterysis, reluctance, back EMF, phase diagrams и т. д. и т. п. Вы не хотите или не должны знать об этом, поэтому мы сделаем это описание простым…
Когда электромагнит (полюс якоря) включается, он не сразу достигает своей полной магнитной мощности. Эта задержка очень мала (миллисекунды), но для двигателя, вращающегося со скоростью 1000 оборотов в секунду, это серьезная проблема.
Для повышения производительности двигателя коллектор “усовершенствуется” – поворачивается дальше в направлении вращения двигателя, – так что питание включается раньше, чтобы достичь максимальной (или, по крайней мере, оптимальной) магнитной силы, когда это наиболее необходимо.
Угол опережения также можно изменить, вращая щеткодержатели в направлении, противоположном вращению. Это дает тот же результат, что и перемещение коллектора. (Новые двигатели Slotworks и Pro Slot имеют регулируемые крышки)
Двигатель с низкими оборотами не требует изменения угла опережения, и в результате он может работать в обоих направлениях – по часовой стрелке или против часовой стрелки с одинаковыми результатами.
Высокоскоростной двигатель усовершенствован для обеспечения оптимальной производительности только в одном направлении и на одной скорости.
Запуск усовершенствованного двигателя задом наперед (т. е. работа с замедлением) в течение любого периода времени — хороший способ превратить его в дым.
Угол опережения, выбранный производителем, также оптимален для набора свойств данного двигателя (сила магнитного поля, длина пакета, витки провода, желаемая частота вращения и т. д. и т. п.).
При торможении двигатель работает как генератор, и ситуация становится обратной; здесь нам нужно было бы уменьшить угол опережения, чтобы улучшить работу “генератора” на определенной скорости.
Таким образом, увеличение угла опережения ухудшает производительность двигателя как генератора – следовательно, меньше «тормозов».
Поэтому нам приходится довольствоваться предварительной настройкой с завода, которая представляет собой компромисс между крутящим моментом на высоких оборотах и торможением. Это лишь один из многих компромиссов, которые необходимо учитывать при проектировании двигателя трассовой модели.
Увеличение угла опережения даст вам больше оборотов и улучшит крутящий момент на высоких оборотах, но приведет к снижению торможения.
Дальнейшее увеличение улучшит мощность на более высоких оборотах, но за счет непропорционального увеличения тока и нагрева, а также потери мощности и крутящего момента на низких оборотах.
Вы можете слишком сильно увеличить угол опережения, то есть перевести коллектор в положение, обеспечивающее эффективную работу двигателя на скорости в 80.000 оборотов в минуту, что просто недостижимо (учитывая мощность двигателя) на гоночной трассе. Это приведет к общему снижению производительности, очень плохому торможению, большому току и, в конечном счете, к задымлению.
Этот мотор может «петь» на столе, но паршиво вести себя на трассе.
Для справки: двигатель Parma 16D, приводящий в движение колеса диаметром 17,5 мм с передачей 10/38 и средней скоростью модели 22 км/ч, вращается в среднем со скоростью 25 343 об/мин, вероятно, достигая пиковых оборотов под нагрузкой 45 000–50 000 об/мин. Без нагрузки он вращается со скоростью около 60 000 об/мин при напряжении 12 В.
При 60 000 об/мин полюсам якоря приходится менять полярность 2000 раз в секунду – быстро!
Если предположить, что производитель правильно выбрал настройку угла опережения (и правильно сконструировал двигатель), то, вероятно, было бы неразумно регулировать угол самостоятельно.
Однако это предположение, вероятно, ошибочно – двигатель Parma 16D номинально производится на заводе с углом опережения 20°, а на практике это значение может отличаться на несколько градусов.
Кроме того, щеткодержатели Parma плохие, а это также влияет на угол опережения, как и многие другие факторы, такие как магниты, предпочтения пилота и т. д.
Щетки двигателя
В трехполюсном двигателе трассовой модели идеальная щетка должна иметь нулевое сопротивление и быть толщиной с бумагу. Даже если бы такой волшебный материал был доступен, он бы просто попал в зазоры коллектора и заклинил двигатель.
Изолирующие канавки в коллекторе должны быть достаточно широкими, чтобы предотвратить прохождение дуги по ним, а щетка, очевидно, должна быть шире, чтобы не проваливаться внутрь.
К сожалению, это обязательное требование, чтобы щетка была шире канавок, приводит к короткому замыканию напряжения на зазоре (оно намного ниже приложенного напряжения).
Даже если бы щетка была очень хорошим проводником, это все равно привело бы к возникновению больших токов короткого замыкания.
Поэтому все щетки изготавливаются с небольшим сопротивлением, что является компромиссом между требованием хорошей проводимости вдоль щетки и плохой проводимостью по поверхности щетки. Щеточная технология – это целая наука.
Таким образом, мы делаем поверхность щетки все шире и шире, что улучшает контакт.
Некоторые думают, что более широкая щетка приводит к увеличению периода включения обмоток, но на самом деле это не так. (Это меняет форму волны приложенного напряжения во время слабых периодов поля, но это выходит за рамки данной статьи и не относится к трехполюсным двигателям, так как сначала происходят другие неприятные вещи)
По мере того, как мы увеличиваем поверхность щетки, мы увидим улучшение производительности двигателя, но в конечном итоге мы достигнем стадии, когда короткие замыкания под щеткой сведут на нет любое улучшение, достигнутое увеличением ширины.
К сожалению, в трехполюсных двигателях мы достигаем точки, когда один сегмент коллектора может коснуться обеих щеток, что приведет к настоящему короткому замыканию (к приложенному напряжению).
Это действительно серьезная проблема, поскольку при сильном коротком замыкании не только не может поступать питание в двигатель, но и существующие магнитные поля быстро разрушаются, увеличивая ток короткого замыкания и эффективно «удлинняя» период короткого замыкания.
Примечание: из-за наличия сопротивления щетки это никогда не является настоящим коротким замыканием. Кроме того, давление под щеткой уменьшается (до косинуса угла) по направлению к краям, причем давление там обычно составляет 75% от давления по центральной линии.
К щеткам типа “Golddust”, “Big Foot” и т. д. предъявляются всевозможные претензии, и они очень хороши – чем больше меди в щетке, тем лучше ее проводимость – чем больше графита, тем меньше проводимость.
Отсюда следует, что чем «чернее» выглядит щетка — тем она более графитовая (и, как правило, дешевле).
Однако у вас может быть ротор, который плохо работает с качественными щетками, такими как “Big Foot”, и лучше работает с «дешевыми» щетками, так как щетки с более высоким содержанием графита доставляют меньше проблем с подщеточными и междущеточными замыканиями.
Однако я бы обычно выбрал щетки с более высоким содержанием меди. Существует несколько очень дорогих составов серебро/медь, которые при определенных обстоятельствах могут быть лучше (смотри предостережения выше), но, вероятно, не подходят в стандартный статор 16D.
См. следующий раздел для технического объяснения проблем с выравниванием щеток.
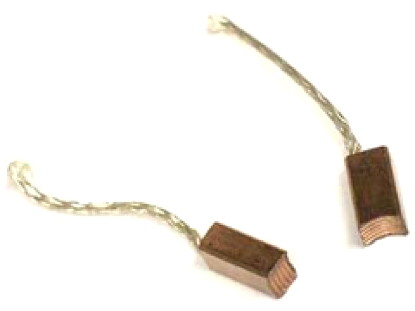
Выше щетки из серебра/меди со встроенными «шунтирующими» проводами – см. раздел «Шунты» ниже.
Технические проблемы с выравниванием щеток
См. рисунок ниже.
Прим. ред.: будьте внимательны – автор статьи считает щетки горизонтальными или вертикальными используя другую логику. В России щетки считаются горизонтальными либо вертикальными наоборот: щетки, расположенные наибольшей стороной вдоль оси двигателя – вертикальные, поперек – горизонтальные.
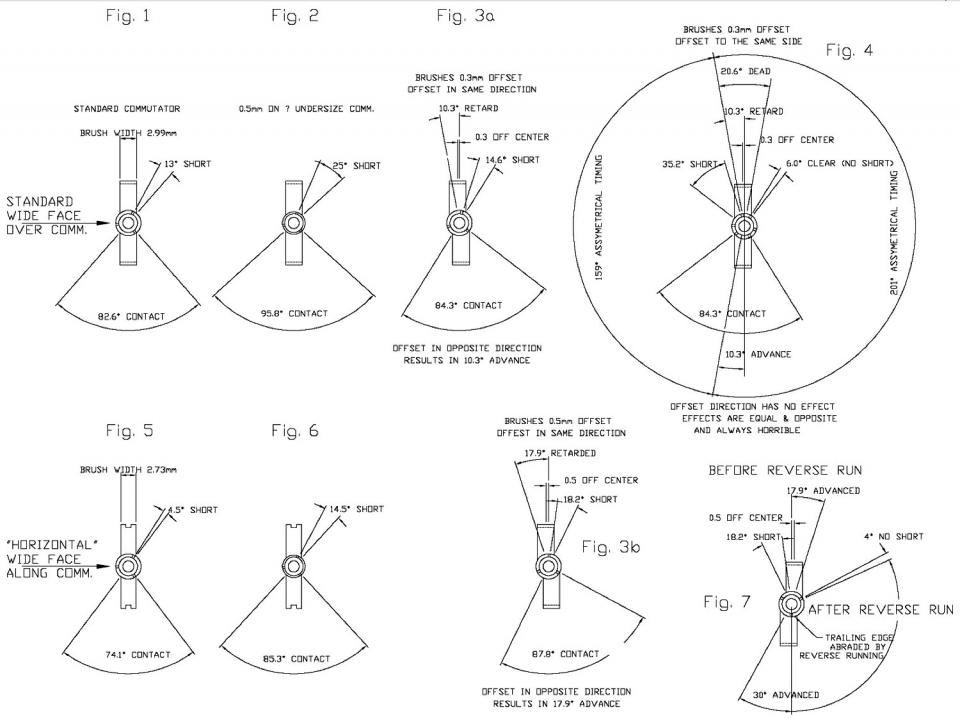
Рис. 1. Показан стандартный коллектор и щетка Parma 16D с использованием широкой стороны щетки в качестве ширины (в некоторых публикациях ее называют «вертикальной» щеткой, т. е. с прорезью в задней части щетки вертикально).
Это дает 82,8° контакта и 13° короткого замыкания – помните, что эти 13° происходят шесть раз за оборот, или в 21,6% времени работы двигателя происходит замыкание – Ааааааа!!!
На рис. 2 показано «горизонтальное» расположение щеток (узкая сторона щетки соответствует ширине), что обеспечивает 74,1° контакта и только 4,5° короткого замыкания или 7,5% времени замыкания двигателя.
Споры о том, какое расположение лучше, в американских публикациях то усиливаются, то ослабевают – я предпочитаю «вертикальное», но использую «горизонтальное» для меньшего (от проточки) коллектора.
Однако настоящая проблема не в этом: щеткодержатели двигателя Parma плохие, и в результате выравнивание щеток ужасное. Маленькие ошибки в выравнивании щеток приводят к огромным ошибкам как в угле опережения, так и в продолжительности коротких замыканий. См. диаграммы и пояснения далее.
Кроме того, если диаметр коллектора уменьшается после его проточки, происходят значительные изменения (см. рис. 2) – коллектор был проточен на 0,25 мм (диаметр уменьшен на 0,5 мм), контакт увеличился с 82,6° до 95,8°, а короткое замыкание увеличилось с 13° до 25°.
Не знаю, как вы, но я не хочу, чтобы мой двигатель замыкался в 42% каждого оборота.
Я бы посоветовал, если вам нужно значительно проточить коллектор, перейти на «горизонтальные» щетки. См. рис. 6. в сравнении с рис. 2.
Одной из наиболее распространенных проблем щеткодержателей Parma является смещение щеток в одну сторону. Из-за большого зазора в щеткодержателях щетки они смещаются в направлении вращения, что также уменьшает угол опережения. При смещении всего на 0,3 мм угол уменьшается на 10,3°, и короткое замыкание увеличивается. При смещении на 0,5 мм наш угол опережения уменьшается на 17,9°, а короткое замыкание составляет 18,2° или 30%.
Очевидно, что при смещении в другую сторону угол опережения увеличивается – это довольно распространенный «обман» для увеличения угла опережения там, где это не разрешено.
Поскольку любой зазор в щеткодержателях (а он должен быть) позволит двигателю слегка наклонить щетку, он всегда будет уменьшать угол опережения и увеличивать продолжительность коротких замыканий.
Вот почему перед гонкой помогает (иногда) ненадолго запустить двигатель задним ходом. Задняя кромка щетки наклоняется в коллектор и быстро истирается, поэтому, когда вы запускаете двигатель правильно, угол опережения увеличивается, а продолжительность коротких замыканий сокращается – по крайней мере, до тех пор, пока щетки снова не прикатаются полностью – см. рис. 7.
И это лишь верхушка айсберга. Дальше – больше.
Все вышесказанное предполагает симметрию. Если же осевая линия щеток смещена в сторону от центра коллектора (см. рис. 4), то все покатилось к чертям.
На рис. 4 мы имеем смещение всего 0,3 мм, но оно приводит к асимметричному приложению мощности, так что на протяжении 20,6° двигатель тянет и толкает одновременно – просто борясь сам с собой! Помните, что это происходит трижды за оборот двигателя.
Плюс у нас есть короткое замыкание на 6° с одной стороны (что нам не помогает) и короткое замыкание на 35,2° с другой (что тоже происходит три раза за оборот). Так что этот мотор закорачивается в 29,3% и “не работает” (но выделяет тепло) в 17,2% времени работы.
Добавим сюда коллектор меньшего размера, и ситуация станет еще хуже – это почти верный путь к тому, что горячая медь покинет ваш ротор.
Из этого следует очевидный вывод: щеткодержатели должны быть очень точно выровнены. Вероятно, это самая важная настройка двигателя вашей модели, поэтому сделайте это правильно.
Если ваши щетки перекошены, они должны быть как минимум симметричными.
Если вы обнаружите, что после установки новых щеток производительность вашего двигателя улучшается, но после некоторого времени использования начинает ухудшаться, то посмотрите на угол контакта на лицевой стороне щетки, когда вы почувствуете, что ваш двигатель работает оптимально (сделайте эскиз). Затем подпилите передний и задний края щетки по этому эскизу всякий раз, когда вы чувствуете, что производительность снижается.
В этом случае рассмотрите возможность перехода с «вертикального» на «горизонтальное» расположение щеток.
Этот переход не так прост, как кажется, поскольку вам нужно модифицировать или расплющить щеткодержатели, чтобы щетки встали ровно и вы точно настроили новую конфигурацию.
В некоторых моторах посадка щеток в щеткодержателях настолько плохая (неплотная), что щетку можно просто повернуть и вставить по-другому– это плохая новость – это просто нелепо– исправьте это. Щетки должны быть выровнены точно.
Двигатель Pro Slot, подробно описанный в разделе Blueprinting, имеет превосходные щеткодержатели и их размещение. Вы не сможете переключиться на другое расположение щеток на этом моторе без модификации или замены щеткодержателей.
Еще один трюк: вы можете удалить материал с задней кромки щетки — сделайте фаску, скажем, 0,5 мм под углом 30°. Это уменьшит эффективную ширину щетки, уменьшит потенциальное подщеточное замыкание и увеличит угол опережения. Аналогично вы можете сделать то же самое на передней кромке щетки — произойдет тоже самое, но с уменьшением угла опережения.
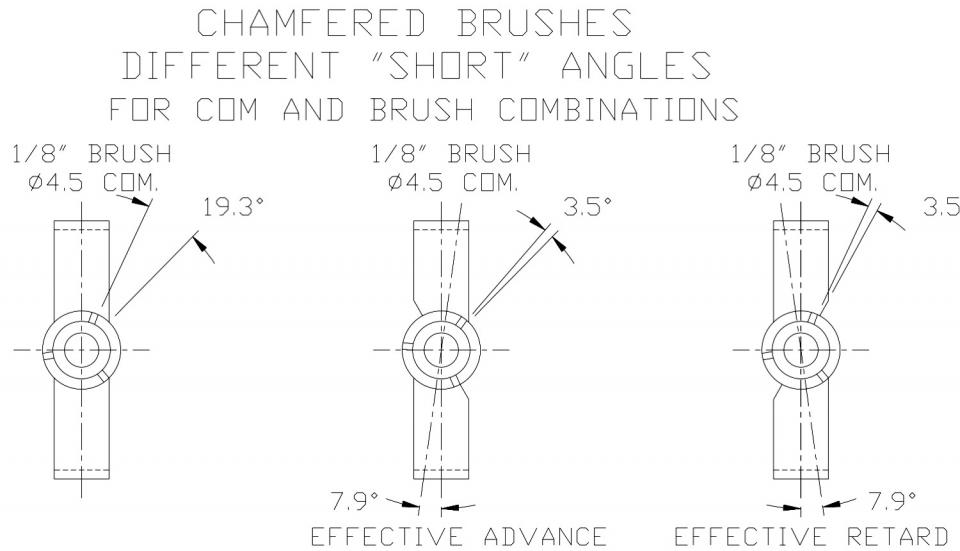
На диаграмме выше показано, как снятие фаски щетки на 0,5 мм под углом 30° может значительно уменьшить угол короткого замыкания, одновременно увеличивая или уменьшая угол опережения в зависимости от того, с какой стороны вы размещаете фаску. (Удаление 0,25 мм с обеих сторон уменьшит угол замыкания, но сохранит угол опережения неизменным.)
Из этого следует, что значительную часть «тонкой настройки» можно выполнить, настраивая сами щетки.
Если вы найдете «настройку», которая работает хорошо, вам придется периодически снимать щетки по мере их износа, чтобы восстановить правильную фаску.
Очевидным недостатком является то, что потребуется частое внимание по мере износа щеток, поэтому он подходит только для спринтерских гонок.
На следующей диаграмме показаны последствия несовершенного выравнивания.
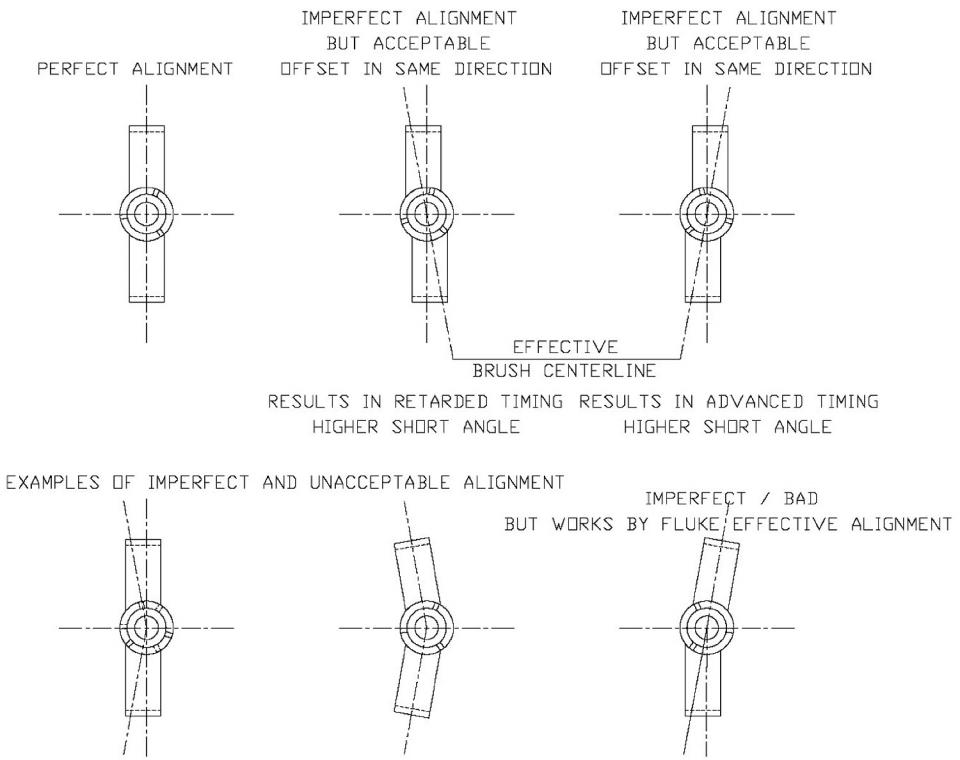
Некоторые двигатели имеют коллекторы абсурдно маленького диаметра (относительно размера щетки). В Parma используются щетки немного меньшего сечения (3 мм, а не более распространенные 1/8 дюйма {3,17 мм}) из-за небольшого коллектора.
Я предпочитаю коллектор большего диаметра для меньшего короткого замыкания на щетках, но это также увеличивает потери мощности на трение щеток – все, что применяется в двигателе трассовой модели, является компромиссом.
На диаграмме ниже показаны различия в углах короткого замыкания для различных комбинаций ширины щетки и диаметра коллектора.
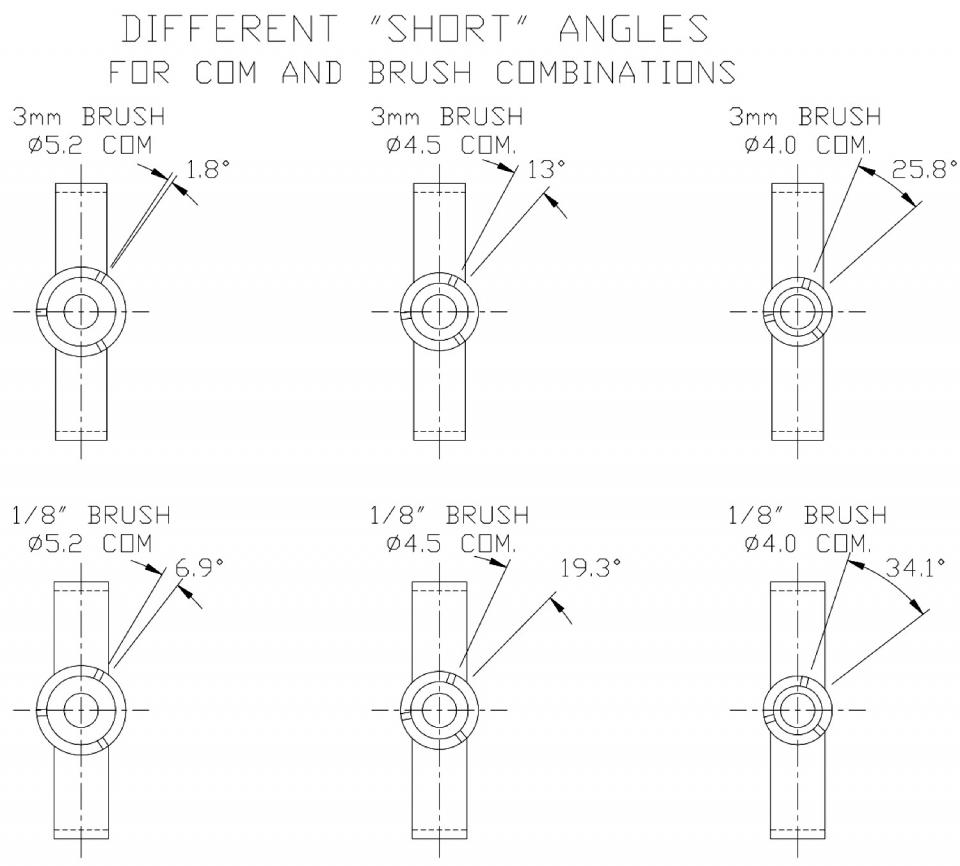
Продвинутые методы
Повторяю примечание: перед модификацией двигателя ознакомьтесь с местными/национальными правилами класса. Нет смысла выигрывать с помощью мошенничества или дисквалифицироваться после победы. Чем больше вы выигрываете, тем интенсивнее становится проверка вашей модели судьями.
Щеточные шунты
Двигатели трассовых моделей могут потреблять много ампер, особенно при пуске, до 10 А для 16D и до 20 А для группы 12, что часто ограничивается блоками питания на трассе до 15-25 А в зависимости от местных правил.
Этот ток может попасть на ротор только через пружину щетки или через фрикционное соединение щетки в ее щеткодержателе. Излишне говорить, что пружина щетки не является хорошим проводником, как и сама щетка или фрикционный характер ее соединения с щеткодержателем.
Нужно отметить, что стенка щеткодержателя будет проводить ток через меньшую щетку, которая ближе к коллектору, но когда она потеряет контакт (что случается часто), ток пойдет через пружину и вниз по щетке (худший возможный сценарий). Кроме того, пружина может нагреться, что усугубит ситуацию, вплоть до того, что она станет мягкой и полностью выйдет из строя.
В некоторых двигателях используется пластиковая пружинная стойка, которая выгорает от перегрева пружины — такие стойки должны быть защищены металлической втулкой. Большинство производителей качественных двигателей теперь используют металлические стойки пружин.
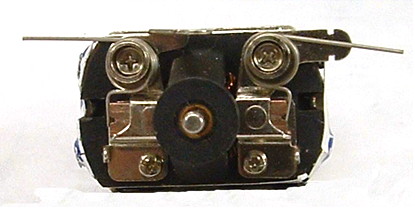
Мотор Pro Slot с алюминиевыми стойками для пружин.
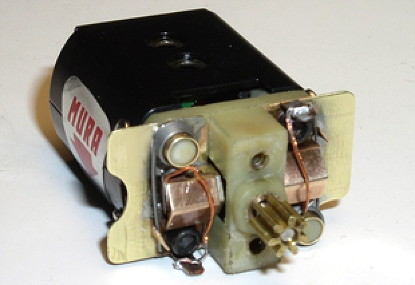
Пластиковые стойки пружин с теплоотводящей втулкой и шунтирующими проводами.
Преимущество использования щеток с присоединенным кабелем (или шунтом) заключается в том, что питание подается непосредственно на щетку и внутрь нее на расстояние ±3 мм (минимальная длина), поэтому это лучше со всех сторон. См. предыдущее фото.
В обычные щетки мы не можем добавить косичку (у меня получилось, но нужен специальный инструмент, а поломки щеток случаются часто — это сложно). Однако мы можем добавить шунтирующий провод от вывода клеммы двигателя к щетке (как на фотографии двигателя Mura выше) — он, очевидно, припаян к выводу, а на щетке он просто зажат под пружиной щетки на одной линии с пружиной.
Вот как можно сделать. Вы, конечно, можете купить готовый провод, но так же легко зачистить кусок старого многожильного гибкого провода.
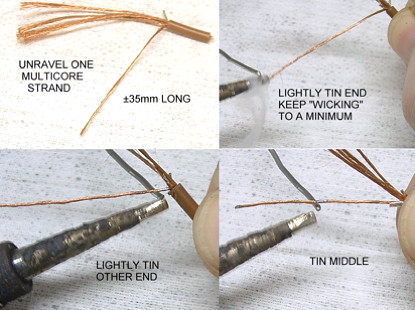
Вам понадобится пара шунтирующих выводов длиной ±13 мм — поэтому начните с длины около 35 мм и пропаяйте их (быстро, чтобы предотвратить «затекание») посередине — да, посередине! Затем как можно легче с обоих концов.
Теперь нам нужно всего лишь 1,5-2,5 мм длины залуженной части для припайки к контакту, поэтому отрежьте припаянный участок провода примерно на таком же расстоянии от места прекращения “затекания”, т. е. проверьте, где провод может нормально сгибаться, и обрежьте его соответствующим образом.
На конце пружины щетки мы обрезаем место, где заканчивается шунт– нам нужен самый минимум припоя, только чтобы шунт не распутался.
Затем добавьте каплю масла чуть ниже паяного конца и дайте ему впитаться — это поможет предотвратить дальнейшее впитывание припоя шунтом, когда мы будем припаивать его к контакту двигателя.
Затем залудите контакт на двигателе – сделайте это, прежде чем пытаться припаять шунт на место.
Затем удерживайте шунтирующий провод чуть ниже припоя плоскогубцами или пинцетом (это также необходимо для предотвращения дальнейшего затекания), а затем быстро припаяйте его к концу контакта ближе к корпусу двигателя, чтобы оставить оставшуюся часть контакта доступным для пайки провода питания, не отпаивая шунтирующий провод, и рискуя получить дальнейшее затекание.
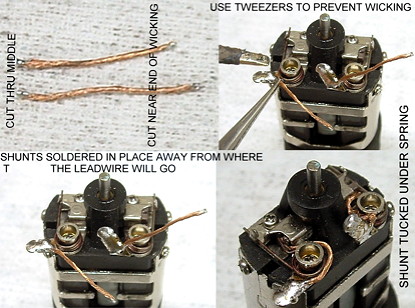
Затем проложите свободный конец к щетке и закрепите пружиной щетки. Убедитесь, что шунт имеет свободный ход и ни за что не зацепляется, особенно при износе щеток.
Также помните, что щунт упрется в щеткодержатель раньше, чем это сделает пружина, поэтому следите за износом щеткок.
В некоторых источниках вам советуют изолировать пружину щетки с обоих концов обмоточным лаком – честно говоря, я не вижу в этом смысла (это нужно для того, чтобы остановить протекание тока через пружину – я иногда так делаю, но при использовании шунта он настолько ниже, что беспокоиться не стоит) – если шунт выпадет, то самое худшее, что может случиться, – это то, что вы вернетесь к обычному пружинному соединению, тогда как, если вы изолируете пружину и шунт выпадет, вы можете остановиться (фрикционное соединение щеткодержателей будет поддерживать работу двигателя, но, как правило, оно работает с перебоями и начинает работать еще хуже, когда это является единственным проводником).
Это ваш выбор.
Это помогает?
Это тот же двигатель, который я использовал на протяжении всей статьи, и позже вы увидите дополнительные кривые мощности на нем (правда он оснащен «голубым» blueprinted ротором от Pro Slot).
Ниже – последовательные испытания с шунтами и без них.
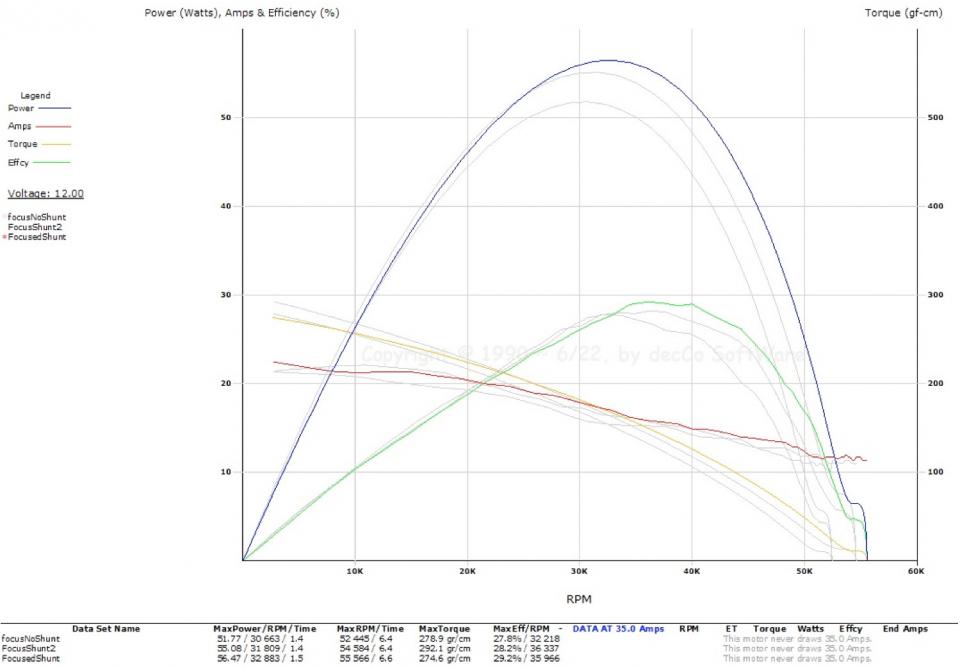
Самая низкая кривая (51,77 Вт) была без шунтов.
Самая высокая (цветная – 56,47Вт) была с шунтами.
Середина (55,08 Вт) с шунтами, но они отпаивалась от выводов. Это показывает, что прирост мощности составил 3,31 Вт (55,08–51,77) из-за увеличенного давления пружины, приложенного из-за шунта под пружиной, а не из-за самого шунта.
Реальный выигрыш от самого шунта составил 1,39 Вт (56,47–55,08) или прирост ±2,5% – конечно, полезно, хотя и не является огромным преимуществом – но, как говорится, важна каждая мелочь.
Щеткодержатели
Эти детали обычно входят в состав ваших щеткодержателей.
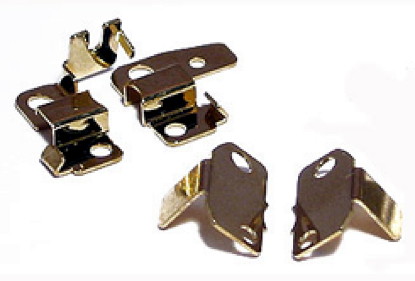
Существуют и другие конструкции, в которых используются гораздо более жесткие обработанные трубки, обычно изготовленные из экструдированной латуни (внешняя сторона шестигранная, квадратное / прямоугольное отверстие), которые обычно припаиваются к опорной пластине для улучшения теплоотвода.
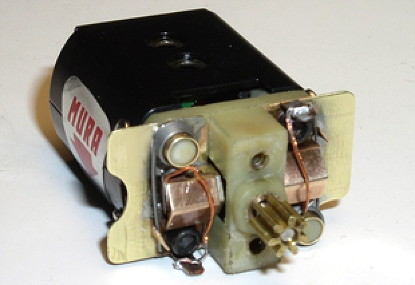
Выше изображен двигатель Mura с цельными трубчатыми щеткодержателями, шунтирующими проводами и увеличенными теплоотводящими пластинами.
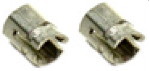
Мощные щеточные трубки
Положение магнитов
Позволит ли перемещение магнитов ближе к ротору повысить мощность и производительность? Для стандартного двигателя короткий ответ – нет.
Вам нужно понять, что происходит – сопротивление обмотки очень низкое, около 0,4 Ом, которое при подключении к 12 вольтам должно составлять 12/0,4 = 30 Ампер – мы знаем, что это не так, но почему?
Когда полюс проходит через магнитное поле, возникает обратное напряжение, противоположное входящему напряжению, так что при (допустим) 60 000 оборотах в минуту индуцированное напряжение составляет 13,8 вольт, а приложенное напряжение – 14,2, так что потребляемый ток составляет (14,2-13,8)/0,4 = 1,0 ампер.
(Это упрощенное объяснение – на самом деле все немного сложнее, и связано с действием электромагнита – на самом деле это устройство переменного тока – несмотря на то, что это двигатель постоянного тока – отдельные полюса постоянно переключаются взад и вперед с относительно высокой частотой. Расширяющийся магнитный пузырь также сопротивляется входящему напряжению.)
Таким образом, если вы переместите магниты внутрь, вы увеличите напряженность поля, и напряжение реакции возникнет раньше – на более низких оборотах. То же самое произойдет, если вы установите более сильные магниты.
Таким образом, усиление поля снижает число оборотов в минуту, а ослабление поля, как бы странно это ни казалось, увеличивает число оборотов в минуту.
Но это еще не конец истории. Если мы перемещаем магниты внутрь / увеличиваем напряженность поля, мы получаем больший крутящий момент, что хорошо, но чтобы компенсировать снижение оборотов в минуту, мы должны уменьшить количество витков, намотанных на наш ротор.
Для данного ротора существует оптимальное положение магнита и его сила, поэтому ротора, намотанные под стандарт 16D, рассчитаны на нормальную напряженность поля. Любое изменение силы или положения магнита должно сопровождаться соответствующими обмотками ротора.
Если бы мы увеличили крутящий момент за счет оборотов, мы не получили бы общего прироста мощности.
Должно быть очевидно, что вы можете получить выгоду от уменьшения магнитного зазора, но, скорее всего, вы этого не сделаете — это потребует слишком много усилий для небольшого прироста.
Тем не менее, при соответствующих обмотках ротора это, безусловно, улучшит производительность.
Ладно, вы не послушались и все равно хотите возиться со своими магнитами…
Уменьшение магнитного зазора
Сначала поймите, что магниты, стакан, магнитный зазор и ротор образуют магнитную «цепь».
Поскольку мы предполагаем, что производитель двигателя изготовил стакан и ротор из 4% SiFe с высокой магнитной проницаемостью, то очевидной точкой наибольшего «сопротивления» магнитной цепи является воздушный зазор (поскольку воздух плохо намагничивается). Магнитное сопротивление называется сопротивлением (reluctance), чтобы не путать его с электрическим сопротивлением (resistance).
Уменьшение этого воздушного зазора увеличит эффективную напряженность поля за счет устранения некоторого сопротивления воздушного зазора.
Примечание: Заливка магнитов эпоксидной смолой практически ничего не даст, поскольку эпоксидная смола обладает такой же проницаемостью, как и воздух, – все, чего вы добьетесь, это переместите зазор с одной стороны магнита на другую. (Правда, благодаря близкому расположению стакана по бокам есть небольшое улучшение. Вполне возможно, что такое небольшое увеличение напряженности поля как раз подходит для вашего ротора – так что некоторые люди будут в восторге от этой модификации, и она часто запрещена правилами клуба – конечно, не помешает попробовать, если это разрешено. Вполне может оказаться, что в вашем двигателе этот метод работает лучше, чем в моем – я больше беспокоюсь о том, чтобы вы понимали, чего пытаетесь достичь.)
То же самое относится и к прокладкам из латуни или нержавейки.
Стальные прокладки от поставщика технических решений – это нормально, но не совсем желательно.
Прокладки должны быть выполнены из 4% SiFe — найдите старый трансформатор и используйте кусочки его пластин в качестве прокладок. (Любые пластины от двигателей, контакторов и т. д.)
Следующая проблема: как далеко в уменьшении магнитного зазора вы собираетесь зайти? Эти двигатели обычно имеют зазор в центре 0,6 мм.
Вы заметите, что кривизна оригинальных магнитов не совпадает с кривизной ротора – даже с учетом большого зазора. Это не ошибка, полюс ротора на самом деле не очень хорошо работает на внешних краях, а увеличение напряженности поля на внешних краях усугубит проблемы короткого замыкания под щеткой, о которых я упоминал ранее. (Дальнейшие примечания по этому поводу см. ниже.)
Если вы уменьшите зазор на 0,5 мм (рекомендуется), то, может быть, вам это сойдет с рук без необходимости «протачивать» или шлифовать магниты.
Это приведет к увеличению радиальной ошибки (см. рисунок ниже) и ненужной фокусировке магнитного поля к центру ротора. Чтобы преодолеть эту проблему, вам необходимо установить прокладку примерно на 0,9 мм и проточить магнитный зазор до диаметра 13,7 мм, чтобы оставить зазор до ротора около 0,1 мм (приблизительно 90° внутренней поверхности магнита).
Еще больше усложняет ситуацию то, что внутренний и внешний радиусы (изогнутой) прокладки одинаковы, поэтому ее толщина различается. Прокладка толщиной 0,5 мм сужается до 0,38 по краям. Прокладка толщиной 0,9 мм сужается до 0,64 мм — вам не нужно придавать ей форму, но если вы этого не сделаете, вы оставите воздушные зазоры, от которых мы и пытаемся избавиться в первую очередь.
Кроме того, необходимо сохранить равномерную форму заточенного отверстия. Оно должно быть параллельным и тщательно отполированным.
Все это очень точная и трудоемкая работа, и, как я уже отмечал ранее, если вы не измените обмотки ротора, ваш результат, вероятно, получится еще хуже (поверьте, я пробовал).
Я не упомянул магнитную регулировку/шлифовку в Blueprinting, поскольку это выходит далеко за рамки «blueprinting» и потому, что я боюсь, что вы создадите больше проблем, чем решите.
Это определенно выводит ваш мотор за пределы класса 16D, поскольку стандартные обмотки ротора 16D не будут работать в этой настройке.
Крошечный зазор также может быть легко забит грязью.
Полировка ротора и магнита приведет к уменьшению аэродинамического сопротивления, но уменьшение воздушного потока и турбулентности приведет к меньшему охлаждению. Тем не менее, большая часть тепла и так передается стакану, и небольшой зазор способствует этому, поэтому я не могу сказать, что когда-либо видел, чтобы это было серьезной проблемой.
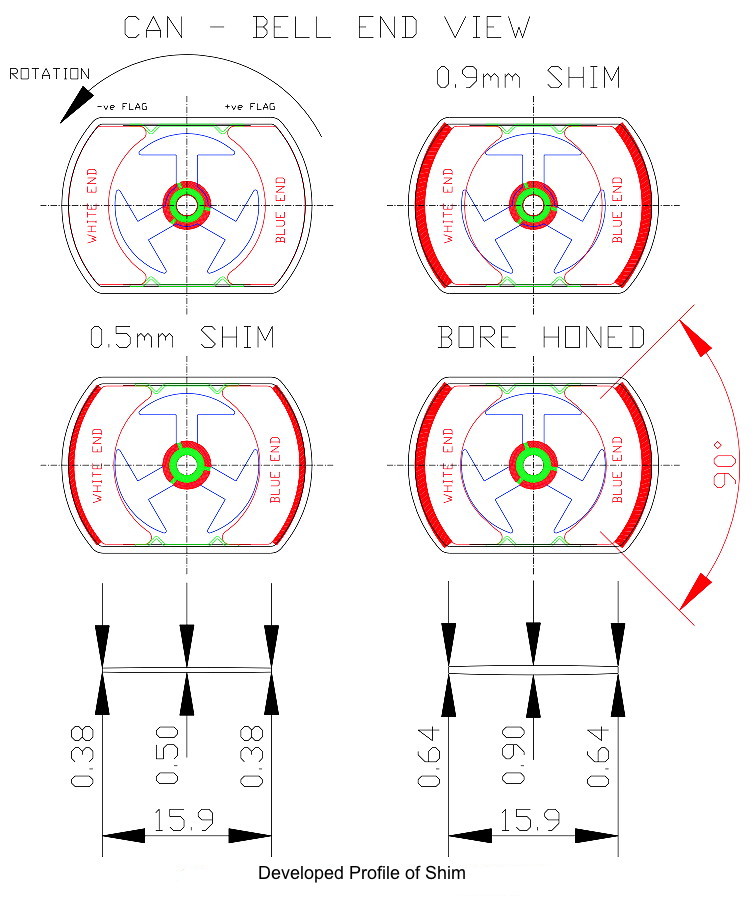
Упомянутая ранее ошибка толщины видна на рисунке выше, где изображена прокладка постоянной толщины.
Вам также может потребоваться удалить заусенцы от точечной сварки на внутренней части стакана или даже «подкорректировать» стакан, чтобы радиусы лучше совпадали (требуется более сложный инструмент).
Прежде чем делать что-либо из этого, вы также можете убедиться, что подшипник скольжения стакана находится в «мертвой точке» по отношению к стакану. (См. Шаг 3 в Blueprinting). Установив вал, измерьте наружный диаметр стакана – если подшипник скольжения смещен от центра, вы можете увеличить его монтажное отверстие – установите подходящую оправку (для установки в корпус или между магнитами), чтобы удерживать подшипник на одном уровне для пайки. Вы также можете установить его в четырехкулачковый или цанговый патрон на токарном станке и обработать припаянный подшипник меньшего размера до истинной мертвой точки и т. д. и т. п.
Если вам нужен более простой способ крепления, вы можете использовать эпоксидную смолу, наполненную железными опилками, или, по моему личному предпочтению, магнитную пыль. Учитывая проблемы с подгонкой прокладок, этот метод работает на удивление хорошо.
Сделайте свои собственные железные опилки/магнитную пыль, измельчив любой подходящий материал (старые пластины ротора, магниты динамиков и т. д.)
Измельчите на алмазном круге на настольной шлифовальной машине – прикрепите неодимовый магнит к подставке, чтобы поймать все опилки.
Смешайте качественную эпоксидную смолу медленного отверждения и добавьте опилки, пока она не превратится в густую пасту – добавьте столько порошка, сколько сможете. Используйте это для приклеивания магнитов на место – используйте макет ротора (или старый ротор – в зависимости от желаемого конечного положения) – обрежьте излишки после отверждения.
Совет: Нанесите разделительный состав на банки и магниты, если вы хотите, чтобы после этого их можно было просто снять или обрезать – позже вы всегда сможете приклеить их суперклеем. Это упростит исправление, если вы все тщательно перемешаете.
Если у вас есть доступ к токарному станку, вы можете сначала покрыть магниты, а затем обрезать их по размеру (что я и делаю).:
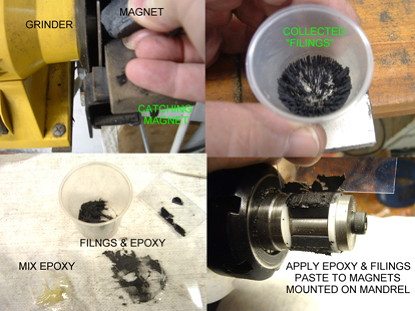
Затем я наношу пасту на заднюю часть пары магнитов и даю ей застыть, затем обрезаю концы и бока напильником и, наконец, поворачиваю внешний диаметр на оправке, специально изготовленной для этой работы. Шайбы из делрина/ацеталя действуют как направляющая/антипригарная поверхность увеличенного размера.
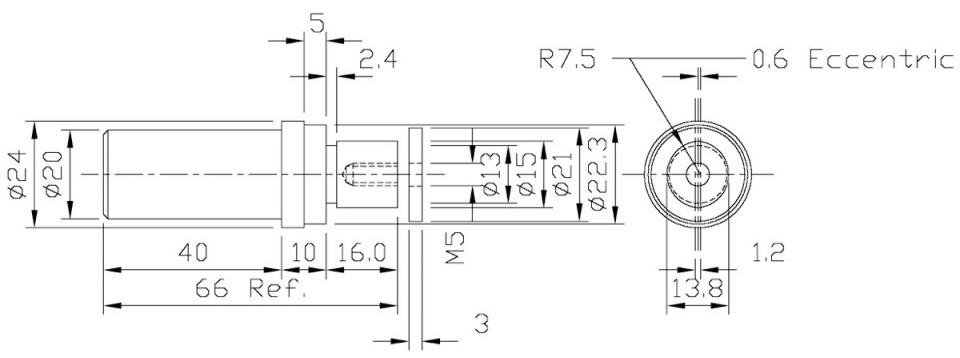
После того, как вы установили магниты и довольны тем, что все хорошо приклеено, без зазоров, и у вас отверстие несколько меньше, чем якорь, теперь вы можете приклеить магниты на место и приступить к «протачиванию» отверстия.
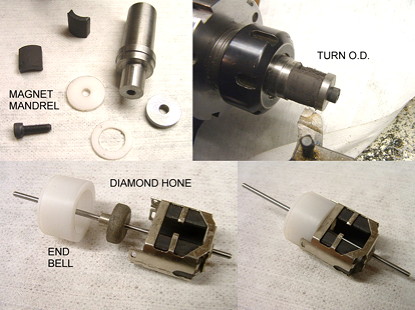
На изображении показана самодельная крышка (end bell), так как шарошка (hone) не всегда входит в зазор щеткодержателей. Такую крышку достаточно легко изготовить, если у вас есть токарный станок.
Вы можете легко различить магнитную пыль/эпоксидную прокладку на магнитах.
Поперечные язычки, удерживающие магниты, загнуты в плоскость. Чтобы загнуть их поверх вставленных магнитов, нужен специальный инструмент. Простое сгибание, скорее всего, приведет к растрескиванию магнитов. Я просто нанес немного припоя на внутреннюю поверхность в качестве фиксатора и надеюсь, что эпоксидная смола сделает свое дело.
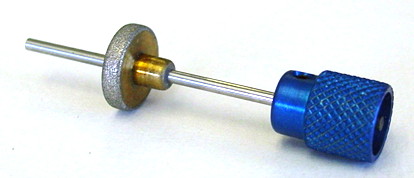
Вверху – шарошка для магнитов с алмазным покрытием (забудьте о ручке, если не хотите стереть пальцы, используйте электродрель / аккумуляторную дрель на низкой скорости). Они доступны в различных размерах у большинства поставщиков комплектующих для трассовых моделей в США.
Вам нужно указать размер – обычно 0,550 дюйма (что даст вам зазор примерно в 0,010 дюйма по сравнению со стандартным ротором).
Я делаю это, погружая в воду для охлаждения/смазки, причем охлаждение более важно, чем смазка. Раньше я использовал легкое масло или парафин, но от воды кажется столько же пользы и гораздо меньше хлопот.
Очевидно, что вы вставляете этот инструмент в стакан и крышку и медленно шлифуете им магнитный зазор. Получается идеально симметричное отверстие.
Магниты и намагничивание
Магниты изготавливаются путем спекания различных материалов с приданием им определенной формы (таких материалов, как феррит, никель, железо, неодим, бор, самарий, кобальт и т. д.). Спекание заключается в сначала смешивании этих материалов в виде очень мелкого порошка (консистенция талька), а затем уплотнение в матрицу под огромным давлением с последующей термообработкой в печи с контролируемым давлением (обычно в вакууме или восстановительной атмосфере) для сплавления некоторых или всех материалов вместе.
В этот момент заготовка не имеет магнитного поля.
Затем заготовку помещают в то, что обычно называют “Magnet Zapper” («магнитным замком») – обычно это магнитная цепь с высокой проницаемостью, в которую помещается заготовка. Обычно концы полюсов сфокусированы на заготовку, а полюсные наконечники полностью соответствуют форме заготовки (относительно предыдущих комментариев о том, что воздушные зазоры снижают силу магнитной цепи), обычно зажимая заготовку на месте без какого-либо зазора.
Magnet Zappers для двигателей трассовых моделей обычно состоят из катушки, корпуса двигателя, магнитов и заготовки-сердечника, расположенной в центре.
Ниже типичный Zapper для двигателей трассовых моделей – обратите внимание на пластиковый держатель стакана двигателя (сторона оси – север – вверх).
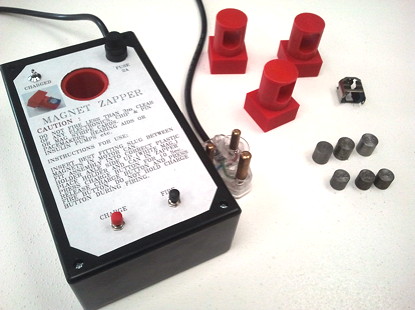
Затем стакан и держатель загружаются в катушку.
При срабатывании Zapper’а огромный импульс электрической энергии из конденсатора разряжается в обмотки вокруг этой магнитной цепи, создавая на короткое время очень сильное магнитное поле, которое постоянно поляризует магнитную(ые) заготовку(и). Вышеупомянутый Zapper выдает 25 000G за 1,5 мс, что достаточно для обратного намагничивания пары керамико-ферритовых магнитов 1200G трассовый модели.
Обычно при этом заготовка насыщается до максимально намагниченного состояния. Поэтому ее максимальная магнитная сила зависит в первую очередь от материала, из которого она изготовлена.
Некоторые составы магнитов, такие как NIB (неодим-железо-бор), могут быть доведены до гораздо более высоких магнитных сил, чем, скажем, керамико-ферритовый тип, но керамико-ферритовый тип менее подвержен размагничиванию и более устойчив к нагреву, чем NIB, таким образом, необходимо выбрать то, что подходит для конкретного применения.
Для двигателей трассовых моделей обычно используется феррито-керамика, поскольку магниты из NIB (хотя и более мощные) с гораздо большей вероятностью размагничиваются под воздействием тепла, механического удара и переменных полей ротора.
Износ магнитов двигателя трассовой модели
Магниты двигателя при использовании подвергаются нагреву (а также нагреву при пайке) и магнитному влиянию ротора, вращающегося внутри них – все это со временем приводит к размагничиванию магнитов.
Двигатель во время работы также имеет тенденцию вытягивать поля магнитов за пределы центра, смещая и расфокусируя их – вы можете заметить последствия этого на двигателе, который «вскипает» без видимой причины. Вы кладете такой двигатель на полку, а два года спустя, отчаянно нуждаясь в моторе, вы снова вводите его в эксплуатацию и обнаруживаете, что теперь он снова работает хорошо (возможно, не так хорошо, как раньше, но определенно лучше, чем когда вы положили его на полку). Произошло следующее: магнитное поле перестроилось, пока оно простаивало. (Оно может перестроиться, но никогда не восстановит свою прежнюю силу.) Такой двигатель можно восстановить, «зарядив» его магниты.
Намагничивание
Имеющиеся в продаже Magnet Zappers доступны для перемагничивания магнитов двигателей трассовых моделей. Обычно это можно сделать несколькими способами:
1) При использовании устройств катушечного типа (показанного выше) корпус и магниты (без крышки и ротора) с заглушкой между магнитами помещаются в немагнитный (пластмассовый) держатель для фиксации сборки в середине магнитного поля катушки. С помощью этого типа намагничивающих устройств у вас нет возможности намагнитить установленный или собранный двигатель (в любом случае это не очень хорошая идея), но они намного дешевле и их удобнее носить с собой, чем устройства с жесткой опорой (которые обычно весят 10-20 кг).
Железная заготовка может представлять собой простой круглый стержень с наилучшим прилеганием к магнитам или профилированную заготовку с двойным радиусом (внутренние радиусы не имеют общего центра). Лучше всего подходит круглый стержень, оставляющий воздушные зазоры на внешних краях, поэтому магнитное поле фокусируется к центру – что в целом хорошо – но общая магнитная сила может снизиться из-за того, что внешние края не насыщаются.
Заготовка с двойным радиусом (полностью повторяющая форму магнитов) создает прямое сквозное поле, которое в целом будет более сильным, но не сфокусированным к середине, где оно принесет наибольшую пользу.
На мой взгляд, лучший метод — круглый стержень, поскольку его простота перевешивает любые сомнительные преимущества.
Примечание. Железная «заготовка» всегда должна быть изготовлена из 4% силикон-железа с высокой проницаемостью. Мягкая сталь — плохая замена (но она отлично работает с ферритово-керамическими типами).
2) При использовании намагничивающих устройств с «жестким полюсом», как и для устройств катушечного типа, магниты помещаются в устройство вместе с имитирующим ротор железным сердечником, чтобы заполнить внутренний диаметр пар магнитов. Зажимы могут соответствовать внешнему радиусу, а сердечник – внутреннему радиусу – с небольшим воздушным зазором или без него. Как вы увидите позже, внутренняя оправка может быть немного меньше, а зажимы — плоскими, что будет «фокусировать» поле к центру магнита.
С помощью этого типа устройств магниты можно намагничивать в стакане, вне стакана, по отдельности, парами или даже весь двигатель – в некоторых случаях даже если он припаян к шасси (если доступ позволяет).
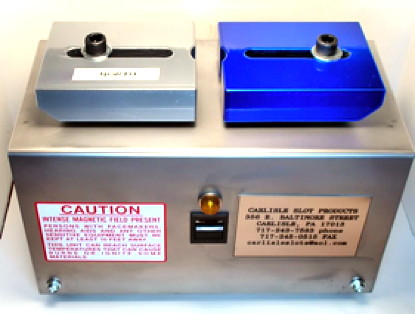
Намагничивающее устройство с «жестким полюсом»
3) Как упоминалось выше, вы можете намагничивать по одному магниту за раз (с соответствующими полюсными наконечниками), но небольшое увеличение магнитного импульса (из-за более короткой магнитной цепи) не обязательно приведет к увеличению мощности магнита, который почти наверняка полностью насыщен (и не станет сильнее). Хуже того, пара, намагниченная в два приема, может иметь смещение поля и проблемы с фокусировкой, поэтому безопаснее намагничивать магниты в виде подобранных пар.
4) Следующий метод – зарядить магниты в корпусе двигателя, при этом ротор на месте и щетки сняты. Если вы не снимите щетки, вероятно, произойдет сильное короткое замыкание (импульсное индуцированное напряжение в обмотках), которое может повредить коллектор и щетки). Это тоже будет мешать «зарядке».
При использовании этого метода у вас есть железный стакан и воздушные зазоры к ротору, которые будут мешать вашей магнитной цепи, а также ограниченное насыщение якоря – поэтому вы, вероятно, не добьетесь полного заряда ваших магнитов. Кроме того, трехполюсный ротор никогда не сможет правильно выровняться с двухполюсными магнитами, поэтому окончательное магнитное поле будет несколько не в форме (см. диаграмму ниже).
Кроме того, ротор станет поляризованным – но это не проблема, поскольку он размагничивается за первые несколько оборотов после раскрутки – из-за быстрого переключения полюсов.
Этот метод рекомендуется использовать только в качестве экстренной меры – однако, если он работает хорошо, значит, он работает. Не стесняйтесь делать это снова, но я не одобряю такой метод.
Приблизительная форма магнитного поля при конформном и неконформном зажиме магнитов в Zapper
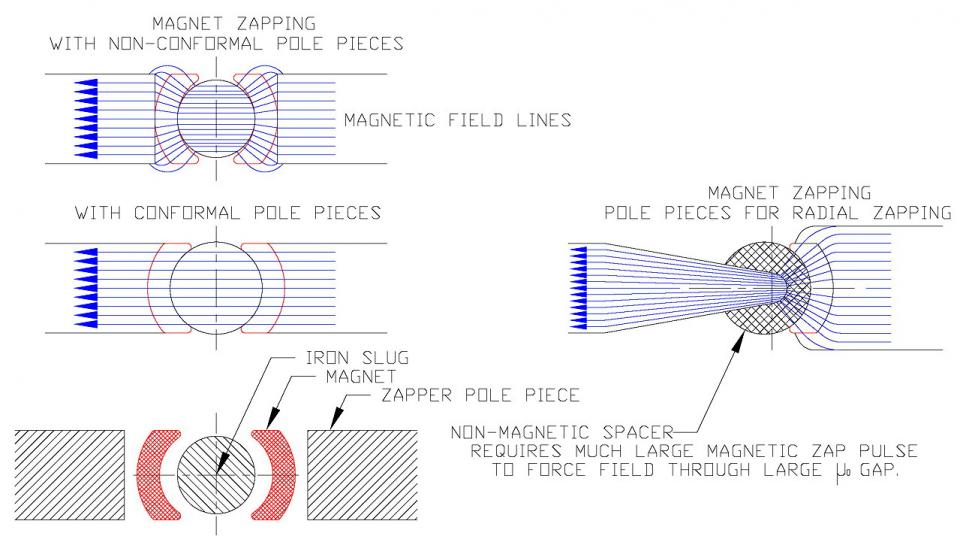
Из вышеизложенного видно, что использование конформных (соответствующих форме магнита) полюсных наконечников и стержней позволяет создавать гораздо более сильную магнитную цепь (за счет устранения воздушных зазоров).
Однако использование простых плоских полюсов (обычно поставляемых в комплекте с устройством) и простого железного сердечника позволяет фокусировать магнитное поле за счет того, что внешние края не полностью насыщаются – это также произойдет в устройстве «катушечного типа», как на фото выше. Поскольку при работе двигателя основная часть выходной мощности ротора (на полюс) находится в центре, а внешние края служат только для увеличения подщеточного короткого замыкания, такая установка, как правило, выгоднее и проще.
Очевидно, что здесь имеет место еще один компромисс в отношении того, насколько высокая степень фокусировки выгодна для снижения общей напряженности магнитного поля. Столь же очевидно, что это можно регулировать с помощью формы зажимных элементов и сердечника – здесь я знаю не больше вашего.
Примечание. Процесс намагничивания магнитов обычно возвращает их в исходное желаемое состояние насыщения; этот процесс, как таковой, не сделает магниты «сильнее».
Внимание: Намагничивающие установки не следует использовать вблизи электронных устройств, устройств хранения данных или ЛЮДЕЙ С КАРДИОСТИМУЛЯТОРАМИ или слуховыми аппаратами. ЭМИ (электромагнитный импульс), испускаемый при срабатывании намагничивающего устройства, потенциально опасен.
Уберите свои цифровые часы, мобильный телефон, планшет, магнитную ленту или кредитные карты с чипом и закрепите их на безопасном расстоянии – как правило, более чем на 3 метра, предпочтительно за стальной экран.
И последнее предостережение – следуйте инструкциям производителя относительно ориентации полюсов. Если вы расположите магниты “неправильно”, их магнитное поле изменится на противоположное (и двигатель будет работать в обратном направлении). Если вы случайно сделали это, исправьте, дважды зарядив в правильном положении – так как одно повторное нажатие может не привести к полному изменению направления поля. Аналогично, если вы решите сохранить случайное изменение направления, вам также следует выполнить повторное нажатие по той же причине.
Хороший Zapper должен быть способен полностью изменить магнитное поле одним ударом.
Четырехполюсные (многополюсные) магниты
Несколько полюсов используются для дальнейшего усиления “фокусировки” и выравнивания магнитного поля в том направлении, где оно принесет наибольшую пользу.
Из приведенной ранее информации следует, что отдельный полюс ротора будет выполнять большую часть своей работы в диапазоне 60° (± 30° от центра магнита), поэтому именно здесь мы хотели бы сосредоточить большую часть магнитного поля – поскольку следующие 60° связаны с подщеточными и короткими замыканиями. И мы вполне были бы счастливы, если бы здесь совсем не было магнитного поля – но, к сожалению, такое невозможно – что еще раз подчеркивает, почему мы хотим «сфокусировать» магнитное поле к центру. Ротор, магнитный зазор и несоответствие радиуса – все это играет здесь определенную роль. Подробнее об этом позже.
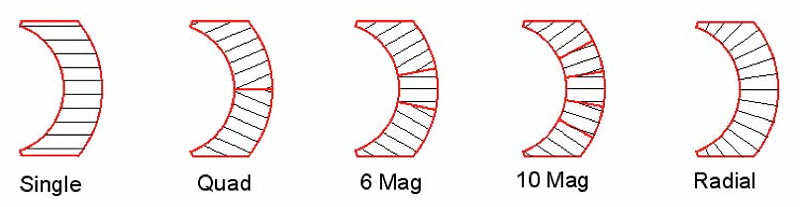
Что должно быть очевидно, так это то, что вы не можете намагнитить несколько полюсных частей, предварительно не разобрав их и не намагнитив по отдельности противоположные пары перед повторной сборкой (обычно они склеиваются вместе или закрепляются на месте специальной эпоксидной смолой). Ну и геморрой!
Поэтому их обычно приобретают у производителя в готовом виде – часто уже установленными в стакан.
Если вы попробуете намагнитить собранный многополюсник, то он снова станет single (моно-магнитом) (состоящим из множества деталей, но, тем не менее, моно-магнитом).
Радиальный магнит получают за счет использования внешнего конформного полюса и небольшой внутренней центральной заготовки с клинообразным/радиусным полюсом (как показано на рисунке выше), однако из–за большого немагнитного зазора (µ0) это требует существенного увеличения мощности, недоступного в большинстве намагничивающих установок.
То же самое потребуется для намагничивания собранных многополюсников.
Вы можете приблизиться к радиальному магниту, используя конформный сердечник в форме “бабочки”, который также подходит для многополюсников, как показано ниже.

Поскольку мощность вашего Zapper’а ограничена, а мы хотим извлечь из этого как можно больше пользы, используйте железо с высокой проницаемостью, сделайте внешние радиусы неконцентричными (наилучший диаметр здесь меньше оптимального, но вы можете сделать это для удобства).
Затем обработайте «V» с обеих сторон — зазор в середине должен быть как можно меньшим — очевидно, он не может быть нулевым, но 1-2 мм было бы неплохо. Однако, ваш Zapper может быть недостаточно мощным, чтобы преодолеть поток импульсного тока, поэтому начните с большего зазора и постепенно уменьшайте. Обычно подходит 3 мм — вы также можете иметь радиус в нижней части «V» — тогда вы можете «вырезать» его, просверлив и затем отпилив ножовкой; грубо, но эффективно, если у вас нет станков.
На чертеже выше материал, подлежащий удалению, закрашен зеленым цветом. Нужно обратить особое внимание на внешнюю поверхность заготовки. Поскольку радиус рабочей поверхности магнита больше, чем радиус заготовки – центры крайних радиусов заготовки не совпадают. Очевидно, что если вы шлифовали свои магниты, это неприменимо; внутренние радиусы магнита соответствуют средней линии.
На каждом этапе намагничивайте пару магнитов, а затем выполняйте намагничивание в обратную сторону. И если полюс меняет направление с полного прямого на полный обратный, то все в порядке и вы можете снять больше материала для уменьшения зазора в сердечнике (>тут<), но в конечном итоге у вас возникнут проблемы (для проверки вам понадобится гауссметр).
Если ваш Zapper вообще не может выполнить разворот магнитного поля, значит, с ним что-то не так — увеличьте его мощность или замените другим. Большинство Zapper’ов можно «поднять», просто увеличив емкость конденсаторной батареи (добавив больше конденсаторов).

На приведенном выше фото – обычные и сфокусированные сердечники – стоят на графике последовательных испытаний двигателей, которые не показывают существенной разницы в выходной мощности.
Однако сфокусированное поле было гораздо более чувствительным к изменениям в ускорении и замедлении – смотрите расширенные испытания двигателя позже. Я не совсем уверен, что с этим делать; у сфокусированного поля на динамометрическом стенде есть лишь небольшое, незначительное преимущество, но при вращении вне динамометрического стенда звук двигателя становится “более диким”. Я предполагаю, что сфокусированное поле оказалось менее подвержено влиянию подщеточных замыканий, но также сузило полку крутящего момента по углу опережения.
Кроме того, с использованием инерционного диска динамометрического стенда нельзя сказать, что двигатель совсем «свободен от нагрузки», и аэродинамическое сопротивление отверстий фотоэлементов становится значительным на высоких оборотах. В результате тот же двигатель c нефокусированным магнитным полем раскручивается без вращения диска до 65 000 об/мин (измеряется оптическим тахометром), в то время как на динамометрическом стенде он достигает максимального значения чуть более 50 000 об/мин.
Двигатель с фокусированным магнитным полем без установленного диска стенда работал со скоростью 67 500 об/мин при напряжении 12,5 В, то есть немного быстрее.
Таким образом, нулевой крутящий момент на динамометрическом стенде означает, что диск больше не ускоряется – двигатель теряет крутящий момент на аэродинамике, а также трении щеток и подшипников скольжения – но в целом исключение этого приведет только к «растягиванию» приведенного выше рисунка и, следовательно, не умаляет фундаментальной пользы динамометрического стенда (более расширенные испытания двигателей позже).
Форма поля
Ниже приведена приблизительная форма поля с установленным ротором, но без вращения и подачи питания.
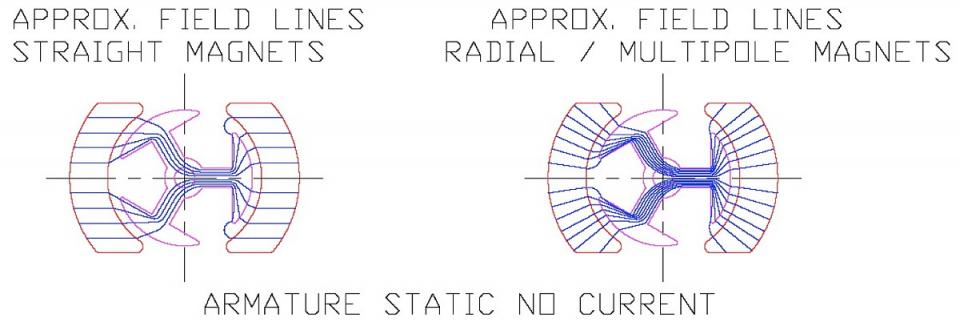
Что должно быть очевидно, так это то, что фокусировка поля является преимуществом, но это преимущество меньше, чем вы могли бы подумать.
Иллюстрация слева должна также объяснить, почему намагничивание двигателя с установленным ротором (вместо круглой заготовки) никогда не приведет к созданию равной и противоположной пары магнитов. Он может создавать сопоставимое общее магнитное поле, но одно будет сфокусировано на середине, а другое на внешних краях, что плохо сказывается на производительности и подщеточных коротких замыканиях, — так что, как правило, это проигрышная ситуация.
Воздушный зазор
В большинстве двигателей трассовых моделей зазор между ротором и поверхностями магнитов в середине меньше, т.е. они не параллельны, радиусы не имеют единого центра.
Это «дешевый» способ фокусировки магнитного поля, но по ужасной цене с точки зрения потери имеющейся напряженности поля. Тем не менее, помните, что двигатель изначально был сконструирован для определенных обмоток, и это было принято во внимание (как мы предполагаем). Но это так же позволяет вам получить больше пользы от имеющихся у вас магнитов с помощью доработки – еще раз напоминаю о необходимом соответствии к обмоткам ротора (см. Положение магнитов).
Итоги по магнитам
Таким образом, мы можем взять существующие магниты, установить на них прокладки, намагнитить и сфокусировать их, прошлифовать и отполировать, и все это может улучшить выходную мощность/производительность нашего двигателя – но только с ротором, подходящим для такого увеличения мощности магнитов.
Также возможно, проделав всю эту работу, получить снижение производительности, что станет полным обломом.
Как правило, я бы посоветовал при использовании стандартного ротора, даже с подготовкой blueprinting, не стоит ничего делать с вашими магнитами, кроме как намагнитить. Однако для некоторых более серьезных роторов, таких как показанный ранее PS700B (“Big Dog”), я считаю почти обязательным повысить магнитные характеристики. Этот ротор определенно имеет меньшее количество витков, чем стандартный, и для этого обычно потребуются «более сильные» магниты.
Мое последнее предостережение по этому поводу: помните, что всегда можно переусердствовать.
Показания Гауссметра
Примечание. Хотя термин Гаусс все еще широко используется, он был заменен в системе СИ на Тесла, где 1G =1×10-4T.
Гаусс относится к силе магнитного поля, создаваемого магнитом – его плотности магнитного потока.
Доступны измерительные приборы, но вы также можете заколхозить его с помощью циркуля или использовать силу отрыва стального шарика, рыболовные весы и т.д. (поищите варианты в сети).
Ниже представлен гауссметр «Spin Doctor» от Go Fast Products.
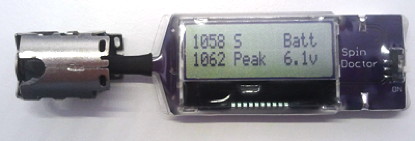
Как уже отмечалось, после подзарядки магнит почти наверняка будет насыщен и, следовательно, будет максимально сильным.
Нас интересует, являются ли наши магниты подходящей парой, и являются ли они сильнее или слабее тех, которые мы обычно используем, или они лучше или хуже после подзарядки и т. д. и т. п. Другими словами, нам нужно только сравнительное значение, а не точный научный результат.
Простой альтернативный метод заключается в том, чтобы положить железный стержень того же диаметра, что и внутренний радиус магнита, но слишком тяжелый, чтобы его можно было поднять с помощью магнита, на цифровые весы – обнулить весы – прикрепить магнит к середине стержня и медленно снимать его – шкала будет становиться все более и более отрицательной – отметьте значение в граммах, при котором магнит ослабевает, и запишите это усилие как показатель его силы. Поскольку это всего лишь сравнительное значение, крайне важно, чтобы вы сохранили этот железный стержень для всех будущих измерений.
Далее нам нужно сохранить совпадающие пары вместе; два магнита в двигателе почти наверняка изготовлены из одной партии смешанных порошков и забиты как пара. Этого нельзя сказать о магнитах, изготовленных с разницей в несколько лет.
Мы можем определить диапазон значений и после намагничивания повторно сопоставить те, которые наиболее точно соответствуют друг другу. Разложить по контейнерам и обозначить их значения.
Теперь мы можем попробовать диапазон от более слабого к более сильному, чтобы увидеть, какой из них дает наилучшие результаты для данного ротора. Помните предостережение, сделанное ранее, о том, что ротор с данными обмотками будет работать оптимально в пределах определенной напряженности поля – более сильное поле не обязательно покажет лучшие результаты.
Потери мощности в двигателе
Потери тепла и мощности в двигателе происходят из четырех источников:
1) Трение: Механическое и аэродинамическое/охлаждающее воздух – устраните, где это возможно, подшипники, выравнивание, уменьшенное давление/трение щеток коллектора, уменьшенный зазор магнитов, полированные якоря/магниты и т. д. См. предыдущие комментарии относительно положения магнитов и напряженности поля.
2) Потери в меди: потери I2R на сопротивлении обмоток – можно уменьшить, используя самый толстый провод, который вы сможете использовать для необходимого количества витков. Единственная альтернатива — серебряный провод.
3) Потери в железе: Потери из-за гистерезисного нагрева и потерь на вихревые токи в железном сердечнике. Их можно уменьшить только за счет использования 4%-ного силиконизированного железа с наилучшей проницаемостью и уменьшения толщины пластин. Двигатели с более тонкими пластинами и короткой длиной пакета из-за этого явления будут терять меньшую мощность. Примечание: для работы при небольшой длине пакета необходимо, чтобы в нем было достаточно железного сердечника – с учетом обмоток и силы магнитного поля.
4) Подщеточные короткие замыкания: Неизбежны в трехполюсных двигателях, но их можно уменьшить за счет правильного материала щеток, настройки пружин и правильного выравнивания щеток.
Расширенное тестирование двигателей
В идеале вам нужно использовать научный метод записи всех ваших изменений и корректировок. К сожалению, это означает, что вы также должны уметь измерять результат.
«Измеряйте то, что измеримо, и делайте измеримым то, что нельзя измерить!» – Галилей, действительно очень мудрый человек!
Обычно это означает тестирование по времени круга на трассе – проблема в том, что оно очень субъективно, и если ваши (как и у мои) водительские способности различаются, и разница невелика, вы не сможете заметить незначительные изменения.
Я видел множество неудачных попыток построить динамометрический стенд для трассовых моделей – коммерческих и других (включая мою собственную «катящуюся дорогу», представленную ниже).
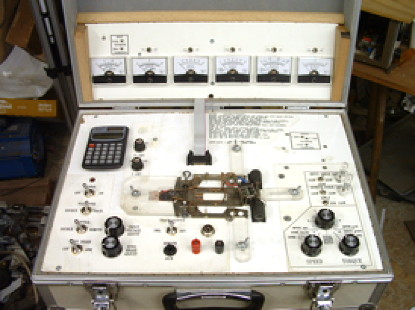
На создание этого устройства потребовалось очень много усилий, это геморрой таскать его с собой, и он полностью аналоговый. Когда оно работает, оно дает лишь краткую информацию и не дает никаких выходных данных. Да, вы можете записать кучу показаний, но, по скольку динамометрический стенд тормозит двигатель, он может очень быстро превратить двигатель в дым.
Сейчас я использую это:
Fantom Racing Products™/deCo SoftWare™ создали динамометрический стенд для трассовых моделей, который действительно работает!
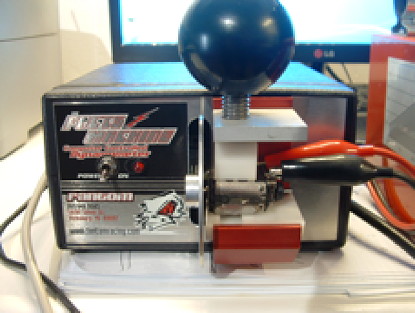
Откуда я знаю, что он работает?
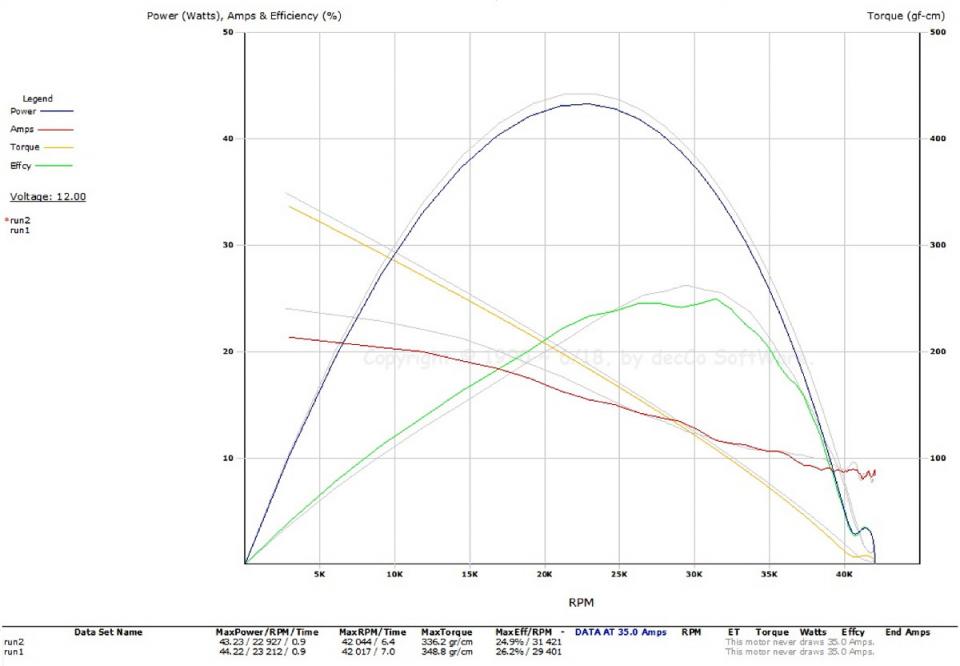
Он обеспечивает повторяемые результаты – я сравнил данные двух тестов одного и то же мотора с интервалом в несколько дней.
Результаты находятся в пределах ±2%, что является лучшей точностью, с которой я когда-либо сталкивался.
Вы можете распечатать график (выше), который был подвергнут алгоритмам сглаживания – также доступен просмотр необработанных данных, а также загрузка (необработанных) данных на рабочий стол, которые можно вставить в Excel и т. д.
Программа не экспортирует графики – изображение выше было создано с помощью клавиши Printscreen (которая помещает копию экрана на рабочий стол), а затем с помощью программы просмотра/редактора фотографий – в данном случае MS Paint – создать – вставить – выбрать область – обрезать – сохранить как *.jpeg.
Стенд работает путем ускорения известной инерционной массы (алюминиевый диск) и мониторинга напряжения, силы тока и ускорения (с помощью фотоэлементов и четырех отверстий в диске), а затем рассчитывает крутящий момент, мощность и КПД, которые отображаются вместе с показателями силы тока на графическом изображении, которые могут быть сохранены во встроенной базе данных.
Вы можете накладывать графики, чтобы сравнить отличия от любых внесенных вами изменений.
Я в полном восторге от этого элегантного набора – он недешевый, но стоит намного меньше, чем я потратил на создание своего собственного, и при этом намного лучше.
Видео на YouTube, демонстрирующее использование динамометрического стенда (на радиоуправляемом двигателе – изначально задуманное использование).
Я не уверен, что эта версия все еще доступна – в Интернете также есть несколько самодельных динамометров, использующих те же принципы.
Прим. ред.: в процессе подготовки перевода данной работы Кена на русский язык мы обнаружили, что статья на форуме SlotBlog не является полной. Недостающие части были найдены в виде PDF-документа на сайте клуба Stolberger Automodell-Club, г. Штольберг, Германия. Однако, изображения в данном документе были подвержены сильному сжатию, сильно снизившему разрешение графиков. Публикуем их как есть, до того момента, пока изображения в лучшем качестве не будут найдены.
Некоторые результаты работы дино-стенда
Следующее относится к двигателю с уменьшением зазора и шлифовкой магнитов, указанному выше, с использованием стандартного 16D «голубого» ProSlot Blueprinted ротора
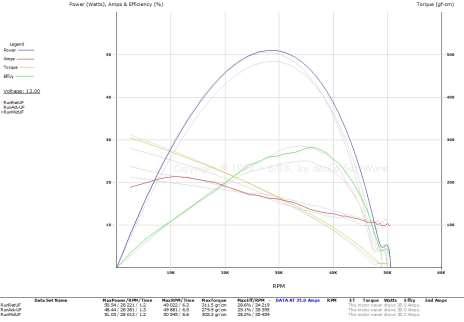
На приведенной выше диаграмме показано «несфокусированное» магнитное поле, цветные линии — с нейтральным положением крышки, верхняя серая кривая — с полностью полным поворотом крышки вперед (для уменьшения угла опережения), а нижняя кривая с полным поворотом назад (для увеличения)— оптимальным будет нейтральное положение (только для этой настройки двигателя – не делайте поспешных выводов).
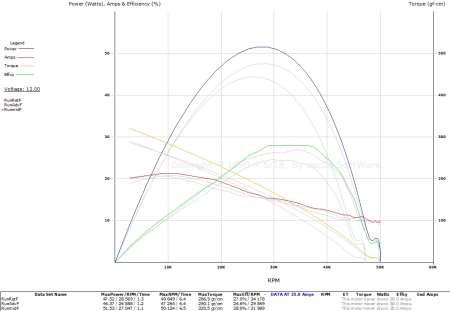
На приведенной выше диаграмме показано «сфокусированное» магнитное поле, цветные линии показаны с нейтральным положением крышки, верхняя серая кривая — с полностью полным поворотом крышки вперед, а нижняя кривая с полным поворотом назад — оптимальным кажется нейтральное положение, но обратите внимание, как гораздо более выражено изменение угла опережения при «фокусированной» сборке.
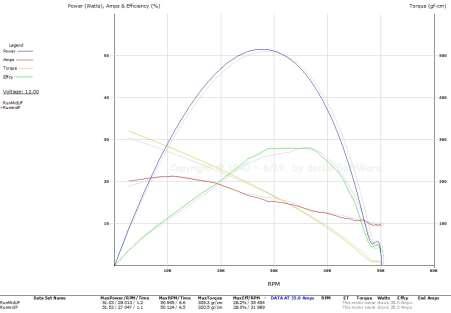
Выше приведено сравнение результатов сфокусированных и несфокусированных магнитов – повторными прогонами – в обоих случаях поле менялось на обратное и возвращалось обратно – никаких других настроек изменено не было.
Разницы нет – (по крайней мере, в пределах точности, так что небольшая разница несущественна) – поди разберись!
Как я уже отмечал ранее, двигатель с сфокусированными магнитами звучал более дико, когда он работал вхолостую, и действительно, он вращался до 67 500 об/мин при 12,5 В по сравнению с 65 500 об/мин двигателя без фокусировки магнитов.
Я думаю, что фокусировка магнитного поля дает лишь очень небольшое преимущество.
Опять же, результаты могут сильно различаться от двигателя к двигателю, особенно если применять его к двигателю, у которого действительно серьезные проблемы с замыканием щеток. И, как обычно это бывает, некоторые люди будут верить в пользу определенных модификаций.
Однако я буду доверять только тому, что мне скажет динамометрический стенд (при условии, что это в целом подтверждается производительностью на трассе).
Ниже приведено динамометрическое сравнение модели Parma 16D “из коробки”, синего ротора Proslot 16D и двигателя, расположенного выше, который был подвергнут магнитной регулировке, намагничиванию, фокусировке полей и установке шунтов.
Это действительно значительное увеличение мощности.
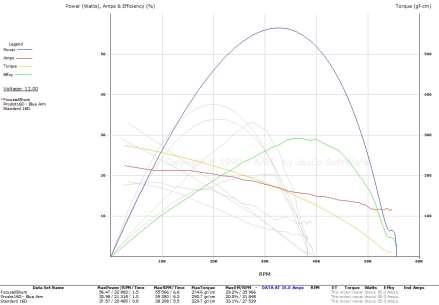
Урок смирения
Я слишком часто видел, как у самого быстрого гонщика в тот гоночный день во время контрольных испытаний обнаруживалась самая маломощная модель.
После недавнего эндуро-заезда “скрупулезная” проверка на дино-стенде показала, что модель команды-победителя (из шести участвовавших в гонке моделей) показала вторую по величине мощность, а команда, занявшая второе место, – самую низкую. Самая мощная модель заняла последнее место! (Очевидно, что более мощный двигатель помогает, но это еще далеко не все
в гонках трассовых моделей.)
Серьезных поломок ни у одной из команд не было, поэтому единственной причиной были умения водителя и подготовка модели (управляемость).
Гонка на выносливость — отличный способ проверить свои результаты в команде на одной модели. Меня всегда чертовски раздражает, что в команде из трех парней, участвующих в гонках на модели, которую я подготовил, я по-прежнему самый медленный гонщик – ужасная правда, которую нужно признать, заключается в том, что двое других парней просто водят лучше, чем я.
Урок: вы не станете победителем, имея только лучший мотор. Подумайте дважды, прежде чем обвинять кого-то в жульничестве.
Расширенная диагностика двигателя
Если у вас есть доступ к осциллографу, подключите клеммы двигателя к осциллографу и включите двигатель в обратном направлении с помощью электродрели или дреммеля – теперь он работает как генератор.
Изучите форму сигнала напряжения, исходящего от двигателя — это должна быть слегка искаженная синусоидальная волна постоянного напряжения (альтернативно выберите фильтр переменного тока на осциллографе, чтобы изолировать компонент переменного тока).
Фактически на один оборот двигателя приходится 6 «ударов», и все они должны быть одинаковыми — если один из трех не работает — это указывает на внутреннее короткое замыкание в этой обмотке — альтернативно, если два из трех не работают, то у вас либо закорочены две обмотки (маловероятно), либо у вас наверняка “вылетел свинец” — этот ротор наверное можно починить перепайкой коллектора.
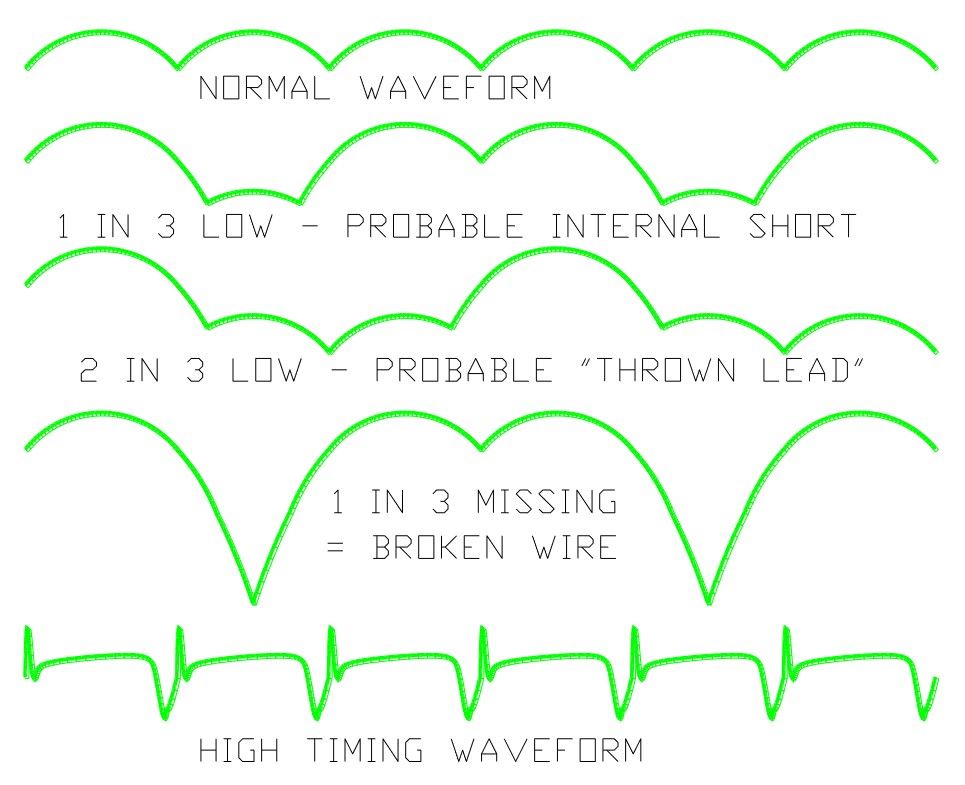
Если один выступ из трех отсутствует, то, вероятно, у вас оборван провод – обычно рядом с проводом (особенно на роторах без бандажа) или даже внутри самой обмотки – что менее вероятно, но возможно.
Если диагностировано внутреннее короткое замыкание или обрыв – ротор пошел навстречу своему производителю – замените или перемотайте.
Часто случается так, что один виток на полюсе может привести к короткому замыканию – тогда это действует как тормоз на производительность двигателя – очевидно, чем больше закороченных обмоток, тем больше проблема.
Одиночный закороченный виток снизит производительность вашего двигателя на 20-30% – до свидания.
Иногда это короткое замыкание проявляется после прогрева, а иногда исчезает сразу после прогрева. Оно также может быть раздражающе прерывистым, например, только на высоких оборотах, так что к концу прямой кажется, что модель “буксует”, что приводит в бешенство.
Одно можно сказать наверняка: дальше будет все хуже и хуже.
Примечание. По мере того, как угол опережения двигателя увеличивается, форма сигнала становится все более и более странной формы с множеством переходных всплесков в точках короткого замыкания и размыкания, обсуждавшихся ранее – условия остаются теми же – все «удары» должны выглядеть одинаково.
Вы также можете «нагрузить» двигатель (при работе в режиме генератора), приложив к нему нагрузку – лампочку автомобильной фары мощностью 40 Вт 12 В или лампочку стоп-сигнала мощностью 20 Вт и т. д.
Вы не можете проверить ротор с помощью мультиметра на наличие чего-либо, кроме грубейших ошибок.
Тестирование с помощью точного миллиомметра (например, манометра Kopriwa) или моста — это шаг в правильном направлении, но в идеале вам необходимо проверить импеданс (сопротивление) при частоте 1 кГц при 12 В.
Несколько плохих примеров
На недавнем клубном 3х часовом эндуро я подготовил 6 blueprinted моторов для бесплатной раздачи 6 командам – две из них решили использовать существующий мотор (поскольку он уже был установлен на шасси – оба были практически новыми) и оставить бесплатный в качестве запасного варианта – у обеих команд он сгорел примерно через 2,5 часа, в то время как мои blueprinted двигатели работали все так же хорошо, а то и лучше, чем на старте. Что и требовалось доказать!
Выгорание №1
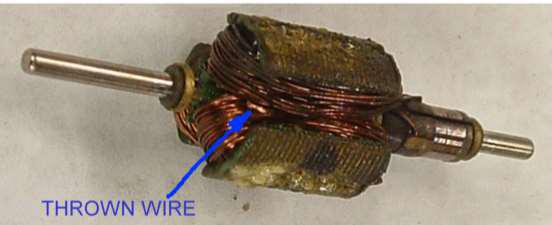
Действительно неопрятные обмотки – очевидно, у него были незакрепленные витки, которые можно было закрепить с помощью лака.
В итоге обмотка вылетела и устроила дым!
Этот ротор также сильно упирался в подшипник стакана из-за неправильного выравнивания магнитов – на внутренней поверхности подшипника был значительный износ, где терлась упорная шайба ротора.
Нечасто увидишь настолько плохо подготовленные моторы, поскольку пилот обычно останавливается, когда видит проблемы с моделью, но в гонках на выносливость они, как правило, давят до тех пор, пока модель не остановится.
Выгорание №2
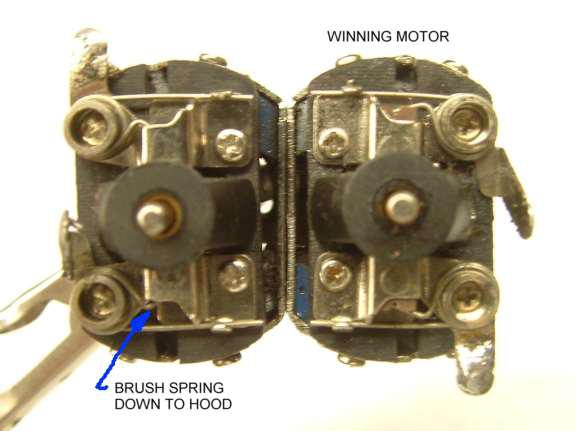
На фотографии выше правый мотор — это “blueprinted” двигатель с модели победившей команды после 3 часов гонок плюс около 30 минут тренировки. Обратите внимание на высоту остатка щеток — вероятно, они проработают еще 4 часа.
Левый двигатель остановился через 2,5 часа, потому что щетки настолько износились, что пружина щетки уперлась в щеткодержатель.
Ладно, на самом деле это не выгорание – но за 30 минут до конца гонки команда (которая была на втором месте) была вынуждена сойти с дистанции.
Разница полностью обусловлена проточкой коллектора. Все blueprinted двигатели перед проточкой показывали отклонение от истинного значения TIR (общего значения индикатора) от 0,02 мм до 0,05 мм. Это может показаться незначительным, но в двигателях с высокой скоростью вращения это приводит к отскоку щеток, что отрицательно сказывается на сроке службы и производительности щеток. Тем более, что двигатель Speed FX оснащен очень качественными, но “мягкими” щетками.
Если вас беспокоит удаление материала с коллектора во время проточки, интересно отметить, что оба коллектора на вышедших из строя двигателях, не подготовленных по blueprinting, были изношены меньше, чем на подготовленном двигателе с проточкой коллектора, который практически не был изношен.
Кривой коллектор НИКОГДА не станет ровным сам по себе – он будет становиться все хуже и хуже. Конечно, работа при низком напряжении в течение длительного времени помогает, но никогда полностью не «округлит» коллектор.
Хотите верьте, хотите нет, но лучший способ прикатать коллектор – это запустить его полностью без нагрузки – это хорошо работает для “пластмасс” – их я запускаю на 15 Вольт в течение 8-16 часов с включенным компьютерным вентилятором, чтобы они охлаждались. К сожалению, двигатели трассовых моделей выделяют слишком много тепла при большом паразитном токе, так что, как правило, это работает не очень хорошо – просто лучше изначально сделать коллектор идеально круглым.
Отскок щеток легко обнаружить: запустите двигатель и понаблюдайте за задней кромкой щетки. Обычно вдоль ее задней кромки видна тонкая синяя подсвеченная линия, вызванная коротким замыканием, когда зазор коллектора выходит из-под щетки.
На правильно проточенном коллекторе это будет слабая однородная синяя линия. Чем больше неровностей на коллекторе, тем шире, ярче, неустойчивее и более «искрящейся» станет линия.
На фотографии ниже вы можете увидеть, насколько сильно изношен коллектор (да, этот ротор сгорел, но несгоревший вышедший из строя неисправный коллектор так же сильно изношен).
Пропайка коллектора
Ранее я упоминал об отличиях обжимных соединений коллекторов от паяных. Мне сообщили, что на самом деле они сварены ультразвуком.
Известно, что сварка меди с медью – сложная процедура, поэтому меня не удивляет, что эффект от нее совсем немногим лучше, чем от механического соединения.
За прошедшие годы я вскрыл несколько таких швов и ни разу не увидел никаких признаков настоящей сварки.
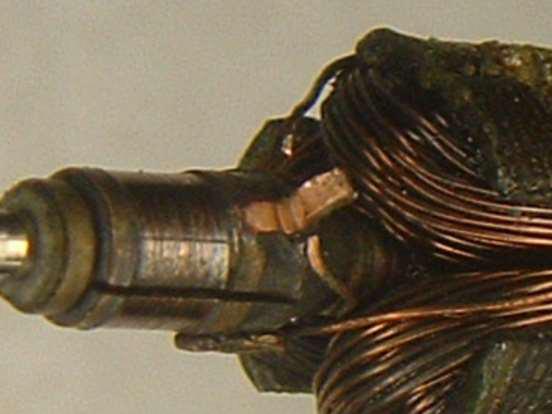
Не самая лучшая фотография, но сварки точно нет, и, что еще хуже, провода пережаты в зажиме. Это повышает напряжение и провоцирует разрыв – особенно при отсутствии бандажа, как в данном случае. Я сломал этот провод, вынимая его.
Может быть, я старомоден, но я предпочитаю припой.
Заключение
Существуют буквально сотни мелочей, которые будут способствовать созданию двигателя с высокой производительностью, и ни одна из них не будет работать каждый раз.
Информация, представленная выше, должна помочь вам принять обоснованные решения при попытке улучшить или исправить двигатель вашей трассовой модели.
Ken Irwin – October 2009
У меня есть подобные статьи в формате MSWord на следующие темы:
- Создание своего собственного блока питания (как показан в статье).
- Создание своего собственного ручного контроллера — на диоде или транзисторе.
- Создание своего собственного Magnet Zapper (как показан в статье).
- Создание своих собственных наклеек.
Если вы хотите что-то из этого – не стесняйтесь обращаться ко мне по электронной почте: keni(sobaka)worldonline.co.za
Автор: Ken Irwin, Южная Африка, Октябрь 2009
Источники: slotblog.net и sac-stolberg.de
Перевод: Андрей Колегов